Introduction to the Certification Exam and Report Purpose
The Grade IV ABC/WPI Wastewater Certification Exam is a rigorous assessment designed to validate the essential competencies of wastewater treatment operators. This examination extends beyond the specific practices of any single system or facility, focusing instead on a broad spectrum of critical job tasks identified through extensive research.1 The exam structure is multifaceted, incorporating various cognitive formats to thoroughly evaluate a candidate’s knowledge and skills. Questions may require simple recall of facts, intricate application of theoretical knowledge to practical scenarios, or precise calculations.1 For instance, an application-based question might ask an operator to explain the necessity of wasting activated sludge, requiring an understanding of process dynamics rather than mere memorization.1
The examination content is typically categorized into several key areas. A significant portion, comprising 42 questions, is dedicated to “Treatment Process Evaluation and Adjustment,” with a strong emphasis on application-based scenarios (35 questions) and a smaller number of recall (7 questions) and calculation items (4 questions). Other important sections include “Equipment Evaluation, Maintenance, and/or Operation” (28 questions), “Laboratory Analysis” (15 questions), and “Security, Safety, and Administrative Procedures” (15 questions).1 Candidates are expected to be familiar with reference materials such as “Operation of Wastewater Treatment Plants, Volume I and Volume II,” and “Operation of Water Resource Recovery Facilities, MOP 11”.2
This comprehensive preparation guide and quiz are specifically tailored to assist candidates in mastering the advanced activated sludge process sections pertinent to the Grade IV certification. The scope encompasses critical areas such as Biological Nutrient Removal (BNR), nitrification and denitrification, sophisticated process control and troubleshooting methodologies, advanced process configurations like Bardenpho, A2/O, and MLE, the intricacies of microbiology and sludge age management, dissolved oxygen dynamics and aeration strategies, secondary clarifier performance, MLSS/MLVSS monitoring and interpretation, and effective responses to sludge bulking and foaming, along with Return Activated Sludge (RAS) and Waste Activated Sludge (WAS) optimization. The quiz questions are meticulously structured to emulate the cognitive formats encountered in the actual exam, including detailed scenario-based troubleshooting questions that demand critical thinking and problem-solving abilities.
To maximize the benefits of this preparation tool, candidates are encouraged to utilize it strategically. Engaging with the quiz allows for the identification of specific areas of strength and, more importantly, areas requiring further study and focused attention. By simulating the question style and depth of content found in the certification exam, this guide aims to build candidate confidence and familiarity with the examination environment, thereby enhancing their readiness for successful certification.
Advanced Activated Sludge Processes: Core Concepts
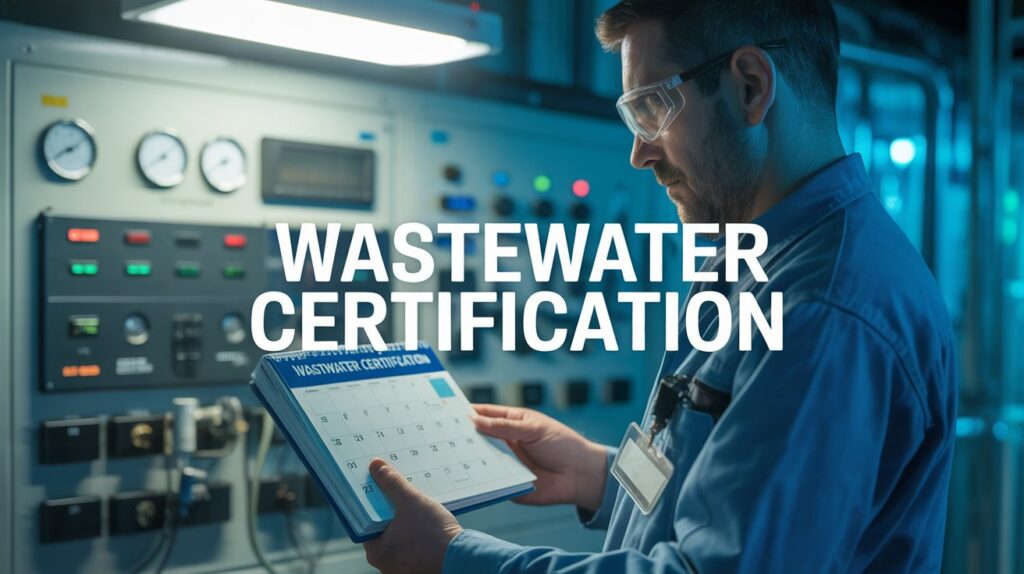
Fundamentals of Activated Sludge for Nutrient Removal
The activated sludge process stands as the most prevalent and effective method for significantly reducing the organic load in wastewater following primary treatment.3 This reduction is paramount, as it directly diminishes the oxygen demand exerted on receiving water bodies, thereby safeguarding aquatic ecosystems.3 Beyond its primary role in carbonaceous biochemical oxygen demand (CBOD) reduction, the activated sludge process is highly adaptable and can be configured to oxidize ammonia and facilitate the removal of both nitrogen and phosphorus from the wastewater stream.3
At its core, the process relies on a series of intricate biochemical reactions. Organic matter, in the presence of oxygen, essential nutrients, and a diverse community of microorganisms, is transformed into new microbial biomass, carbon dioxide (CO2), and water (H2O).3 The newly formed microbial cells, which constitute the activated sludge, are either returned to the aeration basin as return activated sludge (RAS) to continue the treatment cycle or removed from the system as waste activated sludge (WAS) to maintain a balanced microbial population.3 This dynamic recycling and removal of biomass are fundamental to sustaining the efficiency of the activated sludge system.
Key Operational Parameters and Their Significance
Effective control of the activated sludge process hinges upon the precise adjustment and management of several key operational parameters. These include dissolved oxygen (DO) levels, hydraulic residence time (HRT), mean cell residence time (MCRT), also known as solids retention time (SRT), and the rates of return activated sludge (RAS) and waste activated sludge (WAS).3 The manipulation of these parameters allows operators to steer the biological processes towards specific treatment objectives, such as the reduction of BOD, ammonia, total nitrogen, and phosphorus.3
The various control parameters within the activated sludge process are not isolated variables; rather, they are intricately interconnected, forming a complex web of cause-and-effect relationships. For instance, an adjustment in the rate of waste activated sludge directly influences the mean cell residence time (MCRT) of the system. A longer MCRT, achieved by reducing wasting, generally leads to a lower food-to-microorganism (F/M) ratio and can favor the growth of slower-growing nitrifying bacteria, enhancing ammonia removal.3 Conversely, a shorter MCRT, resulting from increased wasting, typically leads to a higher F/M ratio, which can be beneficial for BOD removal but may inhibit nitrification.
Similarly, dissolved oxygen (DO) levels, managed through aeration strategies, have profound impacts on the microbial community structure and activity. While adequate DO is crucial for aerobic processes like BOD removal and nitrification, excessively low DO can promote the proliferation of filamentous bacteria, leading to sludge bulking and poor settling characteristics.5 Furthermore, the energy consumption associated with aeration is a significant operational cost, making precise DO control vital for both treatment efficiency and economic sustainability.7
This interconnectedness means that effective process control necessitates a holistic, systems-thinking approach. Operators must not view adjustments to individual parameters in isolation but rather understand their potential ripple effects across the entire biological and physical system. A change in one parameter can have cascading consequences, influencing microbial population dynamics, sludge settleability, effluent quality, and even energy consumption. A comprehensive understanding of these interdependencies is essential for anticipating unintended outcomes, diagnosing problems accurately, and optimizing overall plant performance to meet stringent discharge regulations consistently.
Biological Nutrient Removal (BNR): Principles and Mechanisms
BNR Definition and Purpose
Biological Nutrient Removal (BNR) represents an advanced technological frontier in wastewater treatment, specifically engineered to eliminate excess nitrogen and phosphorus from municipal and industrial wastewater streams.8 These nutrients, when discharged into natural water bodies, are primary drivers of eutrophication, a process that leads to excessive algal growth, oxygen depletion, and severe degradation of aquatic ecosystems.8 Unlike conventional wastewater treatment methods that primarily focus on the reduction of organic matter (BOD) and suspended solids (TSS), BNR processes harness precise biological mechanisms to address this pervasive nutrient pollution.8 Research indicates the remarkable efficacy of BNR systems, with capabilities to remove up to 90% of nitrogen and 80% of phosphorus from municipal wastewater, underscoring their pivotal role in modern environmental engineering.8
Mechanisms of BNR
BNR systems are characterized by their strategic employment of sequential aerobic and anaerobic conditions, orchestrated through distinct biological treatment stages.8 This cycling of environments is critical for fostering the diverse microbial communities necessary for comprehensive nutrient removal.
The process typically begins with an Anaerobic Phase, where wastewater is introduced into a tank devoid of dissolved oxygen and nitrate. In this low-oxygen environment, specialized bacteria, particularly Phosphorus Accumulating Organisms (PAOs), undergo a metabolic shift. They release stored phosphorus (orthophosphates) into the soluble phase while simultaneously taking up and storing volatile fatty acids (VFAs) or other simple carbon sources, such as acetate, in the form of polyhydroxyalkanoates (PHA) and polyhydroxybutyrate (PHB).8 This initial phosphorus release is a crucial priming step that enhances subsequent phosphorus uptake.
Following the anaerobic stage, the wastewater flows into an Aerobic Phase, where oxygen is actively introduced, typically through aeration systems. This oxygen-rich environment allows a different set of bacteria to flourish and consume the remaining nutrients.8 In this phase, two primary processes occur:
- Nitrification: Ammonia (NH4+) is biologically oxidized to nitrate (NO3-) by autotrophic nitrifying bacteria.
- Phosphorus Uptake: The PAOs, having accumulated carbon sources in the anaerobic zone, now utilize these stored compounds under aerobic conditions to absorb soluble orthophosphates from the wastewater, storing them as polyphosphates within their cells.9 This process significantly reduces the soluble phosphorus concentration in the liquid.
The efficiency of nutrient removal is substantially enhanced by the effective cycling between these anaerobic and aerobic phases, ensuring that the necessary biochemical transformations occur.8 Ultimately, phosphorus is removed from the wastewater stream through the wasting of the activated sludge, which is now enriched with PAOs containing high concentrations of stored polyphosphates.9
Nitrification: Aerobic Conversion of Ammonia to Nitrate
Nitrification is a two-step biological oxidation process that occurs exclusively under aerobic conditions within the activated sludge system.10 This critical process is carried out by specialized autotrophic bacteria, meaning they derive their carbon from inorganic sources like carbon dioxide.11
The first step involves the oxidation of ammonia (NH4+) to nitrite (NO2-). This reaction is primarily facilitated by ammonia-oxidizing bacteria (AOB), such as Nitrosomonas species.10 The simplified chemical equation for this initial conversion is: NH4+ + 1.5 O2 → NO2- + 2H+ + H2O.10
The second step sees the rapid oxidation of nitrite (NO2-) to nitrate (NO3-). This conversion is performed by nitrite-oxidizing bacteria (NOB), notably Nitrobacter species.3 The simplified equation for this reaction is: NO2- + 0.5 O2 → NO3-.10 Under stable operational conditions, these two reactions proceed to completion, resulting in the comprehensive conversion of ammonia to nitrate. The overall biochemical reaction, including the synthesis of new biomass, demonstrates the consumption of alkalinity: NH4+ + 1.83 O2 + 1.98 HCO3- → 0.98 NO3- + 0.021 C5H7NO2.10
For optimal nitrification to occur, the treatment environment must be carefully maintained within specific parameters. Dissolved oxygen (DO) levels are critical, typically requiring concentrations of 2-3 mg/L.3 The pH of the mixed liquor should be maintained within a range of 6.5-8.5, and sufficient alkalinity, generally greater than 50 mg/L as CaCO3, is necessary to buffer the acidity produced during the process.3 Furthermore, nitrifying bacteria are slow-growing, necessitating a relatively long mean cell residence time (MCRT), typically greater than 4 days, with more stable operation often achieved at MCRT values exceeding 10 days.3 Temperature also plays a significant role, with an optimal range for nitrification being 15-30°C.3
A critical consequence of extensive nitrification is its consumption of alkalinity. The overall nitrification reaction explicitly shows the consumption of bicarbonate (HCO3-).10 This alkalinity depletion can lead to a significant drop in the wastewater’s pH, sometimes as low as pH 6, particularly in systems with naturally low influent alkalinity.14 Such low pH conditions can severely impair the overall activated sludge process, often resulting in the formation of “pin floc” (small, poorly settling floc particles) and high effluent turbidity.14 To counteract this, operators must diligently monitor alkalinity and pH. Corrective actions may involve the chemical addition of alkaline agents like lime or soda ash, or the implementation of process adjustments such as on/off aeration or the strategic incorporation of anoxic zones to facilitate alkalinity recovery through denitrification.6 This highlights the necessity for proactive management to maintain stable conditions and ensure regulatory compliance.
Denitrification: Anoxic Conversion of Nitrate to Nitrogen Gas
Denitrification is the biological process responsible for the reduction of nitrate (NO3-) to nitrogen gas (N2), completing the nitrogen removal cycle in wastewater treatment.10 This process is fundamentally distinct from nitrification in its oxygen requirements; it occurs under anoxic conditions, meaning there is very low or no dissolved oxygen present.11
Denitrifying bacteria are heterotrophic, indicating they require an organic carbon source to serve as an electron donor for the reduction of nitrate.11 If the biochemical oxygen demand (BOD) or chemical oxygen demand (COD) levels in the influent wastewater are insufficient to support robust denitrification, external carbon sources such as methanol, acetic acid, or other organic compounds may need to be supplemented to enhance the process efficiency.15
A significant advantage of denitrification is its impact on alkalinity and oxygen balance. The process consumes acid and concurrently produces alkalinity, typically around 3.6 pounds of calcium carbonate (CaCO3) per pound of nitrate-nitrogen reduced.11 This alkalinity generation helps to offset the alkalinity consumed during nitrification, contributing to overall pH stability within the treatment system. Furthermore, by utilizing nitrate as an electron acceptor, denitrifying bacteria effectively “recover” oxygen, estimated at approximately 2.9 pounds of oxygen per pound of nitrate-nitrogen reduced.11 This oxygen recovery can lead to reduced aeration demands in the subsequent aerobic zones, contributing to energy savings.
For effective denitrification, adequate mixing is required within the anoxic zones to ensure complete solids suspension and contact between bacteria, nitrate, and the carbon source, all without introducing dissolved oxygen.11 It is crucial that denitrification logically follows nitrification in the treatment sequence, as nitrate must first be formed before it can be biologically reduced to nitrogen gas.11 The synergistic relationship between nitrification and denitrification in BNR systems is therefore profound. Denitrification not only removes nitrogen, addressing a key environmental pollutant, but also actively contributes to system stability and cost-effectiveness by offsetting the alkalinity consumption and aeration costs associated with nitrification. This dual benefit makes the integration of anoxic zones a highly valuable component of advanced wastewater treatment.
Biological Phosphorus Removal (BPR) Mechanisms
Biological phosphorus removal (BPR) is achieved through the metabolic activity of specialized microorganisms known as Phosphorus Accumulating Organisms (PAOs).9 The BPR process typically involves alternating anaerobic and aerobic conditions to facilitate the unique biochemistry of these bacteria.
In the Anaerobic Zone, PAOs are exposed to a low-oxygen environment where they take up volatile fatty acids (VFAs) or other readily biodegradable carbon sources, such as acetate, from the wastewater.9 To fuel this uptake and the synthesis of intracellular storage compounds like polyhydroxyalkanoates (PHA) and polyhydroxybutyrate (PHB), PAOs hydrolyze their stored polyphosphates, releasing orthophosphates into the bulk liquid.9 This release of phosphorus in the anaerobic zone is a characteristic indicator of effective BPR.
Subsequently, in the Aerobic Zone, PAOs, now laden with stored carbon reserves, are exposed to oxygen. Under these conditions, they utilize their stored PHA and PHB to absorb a significantly larger quantity of orthophosphates from the wastewater than they initially released.9 This absorbed phosphorus is then stored intracellularly as polyphosphates, effectively stripping soluble phosphorus from the wastewater.9 The overall removal of phosphorus from the wastewater stream is accomplished by wasting the activated sludge that is rich in these PAOs, thereby removing the phosphorus contained within their biomass.9
While BPR offers substantial benefits in reducing phosphorus discharge, it inherently leads to an increase in the volume of excess sludge generated during biological treatment.8 This is because the PAOs actively accumulate and store phosphorus within their cellular structure, contributing to the overall mass of the biomass. Consequently, facilities implementing BPR must anticipate and plan for higher sludge volumes, necessitating efficient and robust sludge handling and disposal strategies to minimize environmental impacts.8 This increase in sludge volume represents an operational challenge that must be carefully managed to ensure the overall cost-effectiveness and sustainability of the BNR system.
Benefits of BNR Wastewater Treatment Plants
The implementation of Biological Nutrient Removal (BNR) technology offers a multitude of advantages that significantly enhance the efficacy and environmental performance of wastewater treatment plants.
- Enhanced Nutrient Removal: The most prominent benefit of BNR systems is their superior capability in removing nitrogen and phosphorus compared to conventional treatment methods.8 This leads to a substantial reduction in nutrient discharge into receiving water bodies, directly mitigating the detrimental effects of eutrophication and fostering healthier aquatic ecosystems.8 Studies have demonstrated that the adoption of BNR technology can reduce nutrient loads in urban receiving waters by up to 50%.8
- Cost-Effectiveness: While the initial capital investment for BNR installation may be higher than for traditional treatment plants, the long-term operational savings often provide a compelling economic justification.8 The enhanced biological removal of nutrients reduces or eliminates the need for expensive chemical additions for nutrient precipitation and other downstream treatments, leading to notable reductions in operational expenses.8 Data from the Water Environment Research Foundation indicates that facilities implementing BNR can achieve annual operational cost savings of up to 15%.8
- Regulatory Compliance: BNR systems are instrumental in enabling wastewater treatment facilities to meet increasingly stringent regulatory requirements concerning nutrient discharge.8 Compliance with established limits for nitrogen and phosphorus concentrations, such as those mandated by environmental protection agencies, helps municipalities avoid substantial fines and promotes the overall health and well-being of the community.8
Challenges and Pain Points of BNR
Despite the significant benefits, the implementation and operation of BNR systems are not without their challenges.
- Complexity in Operations: BNR systems demand exceptionally meticulous control over various operating conditions, including temperature, pH, and dissolved oxygen (DO) levels.8 The precise management of these parameters is crucial for optimizing the activity of diverse microbial populations involved in nutrient removal. This inherent complexity can present considerable challenges for facility managers and operators, requiring specialized training and a high level of expertise to ensure optimal conditions for the various microbial processes.8
- Sludge Management: As previously discussed, the increased efficiency in phosphorus removal inherent in BNR processes leads to the generation of higher volumes of excess sludge.8 This necessitates the development and implementation of highly efficient and environmentally sound sludge handling and disposal strategies to minimize the overall environmental footprint of the treatment plant.8
- Infrastructure and Investment: Retrofitting existing conventional wastewater treatment plants with BNR technology often involves substantial capital costs and significant infrastructural modifications.8 Budgetary constraints frequently pose a formidable barrier, preventing municipalities from investing in these advanced systems despite their proven environmental and long-term economic advantages.8
Table 1: Key Operational Parameters for Nitrification/Denitrification
This table provides a concise overview of the critical operational parameters that must be carefully managed to optimize both nitrification and denitrification processes in biological nutrient removal systems. Understanding these distinct requirements is fundamental for effective process control and troubleshooting.
Parameter | Optimal Range/Condition for Nitrification | Optimal Range/Condition for Denitrification | Associated Microbial Group(s) |
Dissolved Oxygen (DO) | Aerobic: 2-3 mg/L 3 | Anoxic: No or very low DO (<0.5 mg/L) 11 | Autotrophs, Heterotrophs |
pH | 6.5-8.5 3 | Generally neutral (6.5-8.0), alkalinity produced 11 | Autotrophs, Heterotrophs |
Alkalinity (as CaCO3) | >50 mg/L (consumed) 3 | Produced (approx. 3.6 lb CaCO3 / lb NO3-N) 11 | Heterotrophs |
Mean Cell Residence Time (MCRT)/Solids Retention Time (SRT) | >4 days, preferably >10 days (slow-growing nitrifiers) 3 | Varies, often longer for combined N/P removal 12 | Autotrophs, Heterotrophs |
Temperature | 15-30°C (optimal for nitrifiers) 3 | Generally higher temperatures increase rates | Autotrophs, Heterotrophs |
Carbon to Nitrogen (C/N) Ratio | Not directly applicable, but sufficient carbon for heterotrophic growth 15 | Sufficient organic carbon (electron donor) required; may need external source 15 | Heterotrophs |
Oxidation-Reduction Potential (ORP) | Positive, typically >+50 mV (aerobic) 15 | Negative, typically -50 to -250 mV (anoxic) 15 | Autotrophs, Heterotrophs |
This table is valuable because it synthesizes critical operational data for two complex, interdependent biological processes into a single, easy-to-reference format. Operators require precise knowledge of the environmental conditions that favor each process. Without this centralized information, they would face the challenge of recalling or cross-referencing multiple parameters from various sources, which is inefficient during real-time process control. By explicitly highlighting the different requirements—for instance, the stark contrast in dissolved oxygen levels between aerobic nitrification and anoxic denitrification—the table underscores the necessity for distinct zones within BNR systems. This clarity aids in diagnosing operational issues where one process might be inhibited due to conditions inadvertently favoring the other, thereby directly supporting the application of knowledge and troubleshooting capabilities essential for the certification exam.
Advanced Process Configurations

Modified Ludzack-Ettinger (MLE) Process: Configuration and Principles
The Modified Ludzack-Ettinger (MLE) process is a widely adopted biological nitrogen removal system that evolved from earlier designs to enhance nitrogen removal efficiency.9 Its configuration is characterized by a sequential arrangement of a completely separated anoxic tank followed by an aerobic tank.9 A defining feature of the MLE process is the internal recycle flow (IRQ), which continuously returns a portion of the nitrate-rich mixed liquor from the aerobic reactor back to the anoxic tank.7 This configuration also includes a secondary clarifier for solids separation, along with return activated sludge (RAS) and waste activated sludge (WAS) lines for biomass management.7
The fundamental principles of the MLE process revolve around the two main steps of biological nitrogen removal: nitrification and denitrification. Nitrification, the biological oxidation of ammonium to nitrate, occurs in the aerobic tank where oxygen is supplied.7 Subsequently, the mixed liquor, now rich in nitrate, is recycled to the anoxic tank via the internal recycle line. In the anoxic tank, denitrification takes place, where denitrifying bacteria reduce the nitrate to nitrogen gas (N2) in the absence of dissolved oxygen.7 These bacteria utilize the readily biodegradable organic compounds present in the incoming wastewater as a carbon source (electron donor) for this reaction.7 The complete separation of these anoxic and aerobic zones, coupled with the internal recycle, provides superior control over wastewater flow and significantly enhances nitrogen removal efficiency compared to earlier, less segregated systems.9
Operational control of the MLE process can be significantly enhanced through advanced automation systems, such as the BIOS system. This integrated hardware and software solution provides real-time monitoring and dynamic control, optimizing the operation of BNR processes.7 The BIOS controller, for instance, calculates optimal dissolved oxygen (DO) and internal recycle flow (IRQ) set-points based on real-time measurements of influent and operating data.7 Optimizing DO set-points directly reduces aeration requirements and increases oxygen transfer efficiency, leading to substantial energy savings, sometimes up to 25% for blowers and 15% for total plant energy.7 Similarly, optimizing IRQ set-points maximizes denitrification performance, minimizes effluent total nitrogen, and maximizes the “oxygen credits” generated in the anoxic zone by reducing nitrate, further contributing to reduced aeration demands and minimizing IRQ pumping energy.7 Typical IRQ rates in MLE processes range from 200% to 400% of the influent flow rate.7 The MLE process is capable of achieving low total nitrogen discharge concentrations, often in the range of 6-8 mg/L, depending on the characteristics of the influent wastewater.7
The integration of process configuration (distinct anoxic/aerobic zones) with sophisticated real-time monitoring and control systems allows for dynamic adaptation to varying loads, leading to substantial energy cost reductions. This demonstrates that the design of advanced activated sludge processes like MLE is not solely about meeting discharge limits; it is equally focused on operational efficiency. The ability to dynamically adjust DO and IRQ based on real-time data allows operators to move from reactive troubleshooting to proactive optimization. This shift in operational paradigm is critical for achieving consistent compliance while simultaneously reducing the largest operational cost in wastewater treatment: energy for aeration.
Anaerobic/Anoxic/Aerobic (A2/O) Process: Configuration and Microbial Roles
The Anaerobic-Anoxic-Aerobic (A2/O) method represents an advanced wastewater treatment process primarily designed for the efficient removal of both nitrogen and phosphorus.9 This configuration is an improvement upon conventional activated sludge processes, featuring a sequential arrangement of three distinct tanks: an anaerobic tank, followed by an anoxic tank, and finally an aerobic tank.13
Each stage within the A2/O process is engineered to provide specific environmental conditions that favor the growth and activity of specialized microbial populations:
- Anaerobic Tank Stage: This initial tank is characterized by the complete absence of dissolved oxygen and nitrates, with agitators ensuring continuous mixing of the activated sludge.13 Under these conditions, microorganisms, particularly Phosphorus Accumulating Organisms (PAOs), become metabolically less active in terms of organic carbon oxidation but are stimulated to release phosphorus into the soluble phase.13 This release is coupled with the uptake and storage of volatile fatty acids (VFAs), preparing the PAOs for subsequent phosphorus uptake in the aerobic zone.9
- Anoxic Tank Stage: Following the anaerobic tank, the wastewater enters the anoxic tank, which also lacks dissolved oxygen but contains nitrate ions recycled from the aerobic tank.13 Here, denitrifying microorganisms, which prefer an anaerobic state, consume the oxygen from these nitrate ions. During this process, nitrate (NO3-) is decomposed, and nitrogen is released into the atmosphere as nitrogen gas (N2).13 This stage is conducive to the growth of typical denitrifying bacteria (DNBs) such as Azospira.17
- Aerobic Tank Stage: The final stage is the aerobic tank, where aeration systems actively introduce oxygen into the water.13 In this oxygen-rich environment, nitrifying bacteria, specifically Nitrosomonas (ammonia-oxidizing) and Nitrobacter (nitrite-oxidizing) bacteria, become highly active.13 They decompose ammoniacal nitrogen, converting it into nitrate ions, which are then circulated back to the anoxic tank to fuel denitrification.13 Additionally, in this aerobic zone, the PAOs that released phosphorus in the anaerobic tank now rapidly absorb excess phosphorus from the wastewater, storing it within their cells.13 The activated sludge, now rich in phosphorus, is then sent to a final settling tank for separation.
The A2/O process typically operates with a Sludge Retention Time (SRT) ranging from 5 to 25 days.12 The microbial community dynamics within the A2/O system are influenced by various factors. While overall microbial alpha diversity can be significantly reduced across the different stages, dissolved oxygen and pH are primary drivers of this diversity.17 Conversely, beta diversity (the difference in microbial communities between samples) is primarily constrained by nutrient conditions such as COD, BOD5, ammonia-nitrogen, total nitrogen, and total phosphorus.17 Studies have also indicated a potential increase in the relative abundance of certain pathogenic bacteria, such as Legionella and Leptospira, across various treatment steps in the A2/O process.17
The explicit sequencing of anaerobic, anoxic, and aerobic tanks within the A2/O process represents a sophisticated engineering approach to wastewater treatment. Each stage is deliberately designed to create distinct environmental niches characterized by specific oxygen conditions, thereby promoting and optimizing the activity of different microbial groups. This deliberate engineering of microbial ecosystems allows for the selection and enrichment of specialized bacteria—such as PAOs for phosphorus removal, and nitrifiers and denitrifiers for nitrogen removal—that efficiently perform targeted pollutant removal. This sophisticated approach to fostering specialized microbial communities is a cornerstone of advanced wastewater treatment, enabling the system to achieve high removal efficiencies for multiple contaminants.
Modified Bardenpho Process: Stages, Flow, and Advantages
The Modified Bardenpho process is a highly effective biological wastewater treatment system specifically engineered for the comprehensive removal of both nitrogen and phosphorus.9 It is characterized by its five distinct reactor stages, each designed to provide precise environmental conditions for optimal microbial activity.
The sequence of these five reactors defines the process flow:
- Anaerobic Reactor: The initial stage where raw wastewater enters. Mixers ensure thorough circulation, distributing carbon and energy sources to the biomass.9 This zone is crucial for biological phosphorus removal.
- First Anoxic Reactor: Effluent from the anaerobic reactor, along with a significant recycle flow from the first aerobic reactor, enters this tank.9 This is where the primary denitrification occurs.
- First Aerobic Reactor: An aeration tank where air compressors supply dissolved oxygen and provide mixing.9 A portion of the effluent from this reactor is internally recycled back to the first anoxic tank.9 This is the main nitrification zone.
- Second Anoxic Reactor: This fourth stage provides an additional anoxic environment. Its purpose is to reduce any remaining or unreduced nitrate that was not recycled to the first anoxic reactor.9
- Second Aerobic Reactor: The final aerobic stage, which further aerates the wastewater to ensure complete nitrification and polish the effluent.9
While gravitational force can drive wastewater flow through some stages, the critical internal recycle flow from the first aerobic zone back to the first anoxic zone typically necessitates pumping to maintain efficient nutrient removal.9 The return activated sludge (RAS) line is connected to the inlet of the anaerobic reactor, ensuring the reintroduction of active biomass.12
The Modified Bardenpho process operates on the core principles of biological nutrient removal, leveraging diverse microbial metabolisms under varying oxygen conditions:
- Biological Phosphorus Removal: This relies on Phosphorus Accumulating Organisms (PAOs). In the anaerobic zone, PAOs take up volatile fatty acids (VFAs) and store them, concurrently releasing orthophosphates into the liquid. In the aerobic zones (first and second aerobic reactors), these PAOs utilize their stored carbon to absorb and store large quantities of orthophosphates as polyphosphates, effectively removing phosphorus from the wastewater.9
- Biological Nitrogen Removal: This involves nitrification and denitrification. Nitrification, the oxidation of ammonia to nitrate, occurs in the oxygen-rich aerobic zones (first and second aerobic reactors).9 Denitrification, the reduction of nitrate to nitrogen gas, takes place in the anoxic zones (first and second anoxic reactors).9 The first anoxic reactor receives nitrate-rich recycle flow from the first aerobic zone, while the second anoxic reactor provides an additional opportunity for complete nitrogen removal.9
The microbial consortium in a five-stage Bardenpho process is diverse, comprising autotrophs (nitrifiers), ordinary heterotrophs (BOD removers and denitrifiers), and PAOs.12 The mass percentages of these populations can vary significantly depending on the characteristics of the primary effluent, such as the TKN/COD and TP/COD ratios.12 The typical Sludge Retention Time (SRT) for a five-stage Bardenpho process ranges from 10 to 20 days.12
The Modified Bardenpho process offers substantial advantages due to its multi-stage design:
- Efficient Nitrogen and Phosphorus Removal: Its primary objective is achieved with excellent nitrogen removal and effective phosphorus removal.9
- Reduction of Other Impurities: Beyond nutrients, the five biological stages contribute to significant reductions in Chemical Oxygen Demand (COD), Biological Oxygen Demand (BOD), Total Suspended Solids (TSS), heavy metals (e.g., nickel and iron), and even viruses.9 Studies have shown high removal efficiencies in practice, with up to 99% for COD, BOD, TSS, and TN, and 90% for TP, along with effective virus removal (average 71.2%) due to adsorption onto biomass flocs.9
- Economical and Operational Benefits: Biological processes in the Bardenpho system substantially reduce the need for consumable chemical compounds compared to chemical or physical methods.9 This, in turn, leads to lower excess sludge volumes.9 The strategic placement of anaerobic and anoxic reactors before aerobic zones also significantly reduces energy consumption compared to conventional activated sludge systems.9 Furthermore, the anaerobic and anoxic zones contribute to improved sludge settling properties, often reflected in a better Sludge Volume Index (SVI).9
The Modified Bardenpho process exemplifies multi-objective optimization in advanced activated sludge configurations. Its intricate design with five stages and multiple recycle loops is not merely aimed at meeting one or two specific discharge limits. Instead, it represents a sophisticated engineering solution that simultaneously optimizes the removal of a wide array of pollutants, including carbon, nitrogen, phosphorus, pathogens, and heavy metals. Concurrently, it strives for significant operational efficiencies, such as reduced energy consumption and lower sludge volumes. This inherent complexity demands a highly skilled operator who possesses a deep understanding of the intricate interplay among biological, chemical, and physical processes within the system. The ability to manage such a multi-faceted process underscores the advanced competencies required for Grade IV certification.
Process Control and Troubleshooting in Activated Sludge
General Troubleshooting Approaches
Operational problems in the activated sludge process typically manifest as issues related to excess foam, high effluent suspended solids, elevated effluent soluble BOD or ammonia, and undesirable low effluent pH.6 Effective troubleshooting often begins with a systematic approach, leveraging direct observations and laboratory analyses. The most effective diagnostic strategy frequently involves microscopic examination of the mixed liquor and oxygen uptake rate (OUR) testing, which are invaluable for pinpointing the fundamental cause of a problem or upset, particularly if it is microbiological in nature.14 Operators are also encouraged to measure physical characteristics, observe visual clues, and analyze the chemical trails left behind by bacteria as they transform pollutants in the wastewater.18
Sludge Bulking and Foaming: Causes and Control Strategies
Sludge bulking and foaming are common operational challenges in activated sludge systems that can severely impact effluent quality and plant performance.
Foaming: Foam accumulation can pose safety hazards by spilling onto walkways or become a regulatory concern if it overflows clarifier surfaces.6 Identifying the type of foam is crucial for accurate diagnosis:
- Pumice-Like Foam: This foam typically appears gray with dark specks and is often caused by solids returned from sludge processing, such as poor solids capture from belt presses or centrifuges, or excess solids in digester supernatant recycle streams.6 The solution involves improving solids capture efficiency within the sludge processing scheme.6
- Grayish, Slimy, Thick Foam: This type of foam is commonly indicative of nutrient deficiencies, particularly nitrogen or phosphorus, and is often associated with a slime bulking condition.6 The corrective action usually involves the addition of the limiting nutrient, such as ammonia to provide nitrogen or phosphoric acid for phosphorus.6
- Dark Brown, Thick, Scummy Foam: This foam is a classic sign of old sludge conditions, frequently caused by the prolific growth of filamentous organisms like Nocardia or Microthrix parvicella.6 These organisms thrive at high MCRT (mean cell residence time) and low F/M (food-to-microorganism) ratios, conditions characteristic of old sludge, and also favor the presence of oils and grease.6 The primary solution is to decrease the total sludge units in the system by increasing the rate of wasting, coupled with the physical removal of foam from the system.6 Once Nocardia has become profuse, it can be particularly challenging to eliminate through increased wasting alone.6
- White, Billowy Foam: This foam is typically caused by high concentrations of surfactants, such as detergents.6 It can occur during system start-up when there is a young sludge with insufficient mixed liquor suspended solids (MLSS) to break the surface tension of surfactant bubbles.6 It can also be found with higher suspended solids concentrations but still not enough to break surfactant bubble surface tension, often due to industrial cleaning processes.6 For start-up conditions, the problem is usually short-lived as MLSS increases. If caused by excessive wasting, decreasing wasting to increase total sludge units is the solution. For high surfactant loads, increasing total sludge units by decreasing wasting and increasing solids detention time in the aerator by decreasing the return flow rate can help.6
Foam is not merely an aesthetic or safety nuisance; it serves as a critical visual diagnostic tool for operators. The distinct characteristics of different foam types—such as color, texture, and stability—immediately signal specific underlying process imbalances. For instance, dark brown, scummy foam points to old sludge and Nocardia issues, while grayish, slimy foam suggests nutrient deficiencies. This direct correlation between foam appearance and underlying cause allows for targeted and effective troubleshooting, moving beyond generic responses to precise interventions. Operators trained to “read” the foam can rapidly identify the root problem, preventing minor issues from escalating into more severe operational disruptions.
High Effluent Suspended Solids: The presence of high suspended solids in the effluent is a common issue, typically resulting from either the discharge of individual particles that fail to settle or a washout of the sludge blanket in the secondary clarifier.6 The initial step in diagnosing this problem is to assess sludge settleability.
- Clarifier Blanket Washout: This occurs when the sludge blanket in the clarifier rises close enough to the surface to spill over the effluent weir.6
- Hydraulic Overload: This is caused by an excessive volume of solids being pushed into the clarifier, which cannot be returned to the aeration tank quickly enough.6 Solutions include decreasing the solids load to the clarifier by initiating step feed or contact stabilization.6 A short-term measure can be to temporarily turn off aeration in the aeration tank to allow solids to settle, reducing the load on the clarifier and enabling the return system to catch up.6
- Return System Overload: In this scenario, the actual solids loading to the clarifier may not be excessive, but the solids are not being returned fast enough, possibly due to a physical obstruction like a clogged return line.6 The solution is to increase the return rate or clean any clogged lines.6
- Poor Settling: Before pinpointing the reason for poor sludge settleability, a diluted settleometer test should be performed.6 If the problem is simply an excessive amount of old sludge in the system, the diluted test will show significantly improved settling.6 The solution for excessive old sludge is to decrease the total system sludge mass by increasing wasting.6
- Individual Particle Washout: If clarifier blanket washout is not the issue, the problem lies with individual particles, which can be tiny pin-floc, large straggler-floc, or individual, dispersed cells.6
- Pin-floc: These are tiny, often dark, pinpoint-sized floc particles associated with very old sludge (low F/M, long sludge age) or chronic toxicity.6 Pin-floc can also be caused by denitrification occurring within the clarifier, where nitrogen gas bubbles buoy floc particles to the surface, leading to “ashing” or clumping.6 Solutions include reducing the MCRT (increasing wasting), increasing return activated sludge (RAS) rates, or implementing on/off aeration or anoxic zones in the aeration tank to shift denitrification away from the clarifier.6
- Dispersed Growth: This involves the growth of individual bacterial cells or very tiny floc, resulting in a very turbid effluent. It typically occurs under very fast growth conditions (high F/M) or in the presence of toxic loads.6 The corrective action is to reduce the F/M ratio (usually by increasing the MLSS concentration), increase total sludge units, and decrease wasting and return rates.6
Sludge Bulking: Sludge bulking is a widespread and serious operational challenge in activated sludge processes, defined by sludge that settles and compacts slowly, often characterized by a Sludge Volume Index (SVI) greater than 150 mL/g.14 Severe bulking can lead to the loss of sludge inventory to the effluent, causing environmental damage and permit violations.14 While an appropriate amount of filamentous bacteria can be beneficial, providing a “backbone” to floc structure and improving settling, problems arise when these filaments grow in excessive quantities, hindering sludge settling and compaction.14
The causes of filamentous growth and bulking are diverse and often specific to certain operational conditions or influent characteristics:
- Low Dissolved Oxygen (DO) Concentration: This condition favors the prolific growth of filamentous organisms such as Sphaerotilus natans, Type 1701, and Haliscomenobacter hydrossis.14 The primary solution is to increase the dissolved oxygen levels in the aeration basin.6
- Low F/M (Food-to-Microorganism Ratio): A low F/M ratio, indicative of old sludge, can promote the growth of filaments like Type 0041, Type 0675, and Type 1851.14
- Septicity (Sulfide Presence): The presence of sulfide in the wastewater can lead to the growth of sulfide-oxidizing filaments such as Thiothrix, Beggiatoa, and Type 021N.14 Control strategies include removing the sulfide source, preaeration to oxidize sulfide, or adding iron compounds (e.g., ferric chloride) to chemically bind sulfide.6
- Grease and Oil: High concentrations of grease and oil in the influent can promote the growth of Nocardia and Microthrix parvicella, which are known to cause bulking and foaming.14
- Nutrient Deficiency (Nitrogen or Phosphorus): A lack of essential nutrients can lead to the proliferation of specific filamentous organisms like Type 021N, Thiothrix, Nostocoida limicola, Haliscomenobacter hydrossis, and Sphaerotilus natans.14 The solution involves increasing the nutrient levels in the wastewater.6
- Low pH: Extremely low pH conditions can favor the growth of fungi, which can contribute to bulking.14 Increasing the pH by adding caustic or buffer solutions is the corrective action.6
- Readily Metabolized Substrate: Rapidly metabolizable short-chain organic acids (often from industrial influent or anaerobic selectors in BNR systems) can promote the growth of filaments such as Type 1851, Type 021N, and Nostocoida limicola.6 Pretreatment to remove the organic acid source or the implementation of an appropriate selector (aerated, anoxic, or anaerobic) can mitigate this.6
- Slowly Metabolized Substrate: Filaments like Type 0041, Type 0675, and Microthrix parvicella thrive on slowly metabolized food, often associated with older sludges.6 Maintaining good mixing and proper DO throughout the aeration basin, and often reducing the MCRT, can help control their growth.6
- Surface Seeding: Organisms growing on upstream surfaces (e.g., pipes, attached growth systems) can slough off and seed the aeration tank with filaments, including Sphaerotilus natans, Thiothrix, and Beggiatoa.6 Ensuring adequate DO and removing sulfide in the upstream process can help prevent this.6
The importance of microscopic analysis as the foundation of troubleshooting cannot be overstated. Multiple sources emphasize the critical role of microscopic examination and oxygen uptake rate (OUR) testing in diagnosing activated sludge problems, particularly bulking and foaming.6 The detailed identification of filamentous organisms and their specific causes underscores the value of this diagnostic tool. Microscopic analysis provides direct, real-time insights into the biological health and composition of the activated sludge, allowing operators to precisely identify the root cause of complex issues like bulking. This precision enables the implementation of targeted and effective control strategies, moving beyond trial-and-error approaches that can often exacerbate problems, and ultimately ensuring more efficient and compliant plant operation.
Addressing Nitrification and Denitrification Problems
While nitrification and denitrification are vital for nutrient removal, their operational requirements can sometimes lead to specific problems within the activated sludge process.
- Low Effluent pH: A common issue is a significant drop in effluent pH, sometimes as low as pH 6, caused by extensive nitrification.14 This occurs because nitrification consumes alkalinity, particularly problematic in wastewaters with low natural buffering capacity.14 Such low pH can lead to operational upsets like pin floc formation and high effluent turbidity.14 Solutions include the chemical addition of alkaline agents such as lime, soda ash, or sodium bicarbonate to raise the pH.6 Alternatively, process adjustments like on/off aeration or providing an anoxic zone can help return enough alkalinity to raise the pH by promoting denitrification.6
- Floating Sludge/Ashing in Clarifier: This problem arises when denitrification occurs inadvertently in the final clarifier.14 Bacteria in the settled sludge utilize nitrate as an electron acceptor in the absence of dissolved oxygen, producing nitrogen gas (N2) as a byproduct.14 These small, slightly soluble nitrogen gas bubbles become entrapped within the sludge floc, making clumps of sludge buoyant and causing them to float to the surface (known as “ashing” or “gassing”).14 This phenomenon is more prevalent in warmer months and can be exacerbated by filamentous sludge, which provides a better matrix for gas bubble entrapment.14
To control denitrification in the clarifier, several strategies can be employed: reducing the total sludge units in the system by increasing wasting, which limits the amount of nitrate-rich sludge entering the clarifier 14; increasing return activated sludge (RAS) rates to remove sludge faster from the clarifier before significant denitrification can occur 14; or increasing the dissolved oxygen concentration in the final clarifier, particularly at the clarifier end of the aeration basin, to prevent anoxic conditions.14 In severe cases, hydrogen peroxide can be added directly to the center well of the final clarifier as an oxygen source to suppress denitrification.14
The management of nitrification and denitrification requires a delicate balance of competing demands. Nitrification consumes alkalinity and necessitates a high dissolved oxygen environment, while denitrification produces alkalinity and requires anoxic conditions. Problems such as low pH or floating sludge in the clarifier arise when these processes are not properly balanced or occur in unintended zones.14 Operators must meticulously manage dissolved oxygen levels and sludge age to ensure that nitrification and denitrification occur in their designated zones, thereby preventing undesirable side effects in the clarifier or pH imbalances throughout the system. This continuous optimization challenge underscores the need for precise process control in BNR systems.
Table 2: Common Activated Sludge Foaming Issues and Solutions
This table serves as a practical guide for diagnosing and addressing common foaming problems in activated sludge systems, linking visual observations to their underlying causes and recommended operational responses.
Foam Description | Primary Cause(s) | Associated Organisms (if applicable) | Recommended Operational Solution(s) |
Pumice-Like Foam (Gray with dark specks) | Solids returned from sludge processing (e.g., poor capture from dewatering, excess digester supernatant) 6 | – | Improve solids capture in sludge processing scheme.6 |
Grayish, Slimy, Thick Foam | Nutrient deficiencies (nitrogen or phosphorus), often with slime bulking 6 | – | Add limiting nutrient (e.g., ammonia for N, phosphoric acid for P).6 |
Dark Brown, Thick, Scummy Foam | Old sludge conditions (high MCRT/low F/M), presence of oils/grease 6 | Nocardia, Microthrix parvicella 6 | Increase wasting to decrease total sludge units; physically remove foam from system.6 |
White, Billowy Foam | High surfactant loads (detergents) 6 | – | For young sludge/start-up: Decrease wasting to increase total sludge units. For high surfactant loads: Decrease wasting to increase total sludge units, and decrease return flow rate to increase solids detention time in aerator.6 |
This table is highly valuable as a practical troubleshooting guide for operators. Foaming is a frequently encountered and visually obvious problem that can impact plant aesthetics, safety, and effluent quality. By presenting distinct foam characteristics alongside their specific causes and solutions, it enables operators to perform rapid and accurate diagnoses. This structured approach facilitates targeted intervention, moving beyond generic “reduce foam” actions to precise process adjustments. Such systematic problem-solving is crucial for efficient plant operation and for preventing minor issues from escalating into more severe operational challenges or compliance failures.
Table 3: Sludge Bulking Causes and Filamentous Organisms
Sludge bulking is a critical operational issue that impairs solids settling and can lead to effluent violations. This table provides a structured overview of common causes of bulking, the filamentous organisms typically associated with each cause, and general control strategies.
Primary Cause of Bulking | Key Filamentous Organisms Associated | General Control Strategy |
Low Dissolved Oxygen (DO) Concentration 14 | Sphaerotilus natans, Type 1701, Haliscomenobacter hydrossis 14 | Increase DO in aeration basin.6 |
Low F/M (Food-to-Microorganism Ratio) 14 | Type 0041, Type 0675, Type 1851 14 | Increase F/M (e.g., reduce MLSS, increase organic load if possible).6 |
Septicity (Sulfide Presence) 14 | Thiothrix, Beggiatoa, Type 021N, Type 0914 14 | Remove sulfide source; preaeration; add iron compounds (e.g., ferric chloride).6 |
Grease and Oil 14 | Nocardia spp., Microthrix parvicella, Type 1863 14 | Control grease/oil influent; increase wasting and foam removal.6 |
Nutrient Deficiency (N or P) 14 | Type 021N, Thiothrix I and II, Nostocoida limicola III, Haliscomenobacter hydrossis, Sphaerotilus natans 14 | Increase nutrient levels (e.g., add ammonia, phosphoric acid).6 |
Low pH 14 | Fungi 14 | Increase pH by adding caustic or buffer solution.6 |
Readily Metabolized Substrate (short-chain organic acids) 6 | Type 1851, Type 021N, Nostocoida limicola, H. hydrossis, S. natans, Thiothrix 6 | Pretreatment to remove source; implement appropriate selector (aerated, anoxic, or anaerobic).6 |
Slowly Metabolized Substrate 6 | Type 0041, Type 0675, Type 0092, M. parvicella 6 | Maintain good mixing and proper DO; reduce MCRT.6 |
Surface Seeding 6 | Sphaerotilus natans, Thiothrix, Beggiatoa, fungi, Type 1701 6 | Ensure adequate DO; remove sulfide; create unfavorable environment for filament growth upstream.6 |
This table is invaluable for operators dealing with sludge bulking, a pervasive and challenging issue that can severely impact effluent quality and plant capacity. It provides a structured framework for understanding the diverse causes of bulking, directly linking them to the specific filamentous organisms that can be observed microscopically. This organized information is crucial for correctly identifying the root cause of bulking, which, in turn, enables the implementation of the most effective control strategies. By allowing for precise diagnosis rather than trial-and-error approaches, which can often exacerbate the problem, this table reinforces the importance of microscopic analysis as a fundamental diagnostic tool in activated sludge process control.
Microbiology and Sludge Age Management

Key Microbial Populations in Activated Sludge
The activated sludge process thrives on a complex and dynamic ecosystem of microorganisms residing within the aeration basin. This diverse community is the biological engine of wastewater treatment, responsible for the breakdown and transformation of pollutants.3 The primary constituents of this microbial population include flocculated bacteria, various species of fungi, protozoa, and rotifers.3
Within this diverse consortium, several key functional groups of bacteria play distinct and vital roles:
- Autotrophs: These are self-feeding bacteria that obtain their carbon from inorganic sources, primarily carbon dioxide. In the context of activated sludge, the most significant autotrophs are the nitrifying bacteria, specifically Nitrosomonas (ammonia-oxidizing bacteria, AOB) and Nitrobacter (nitrite-oxidizing bacteria, NOB). These organisms are solely responsible for the biological oxidation of ammonia to nitrate, a critical step in nitrogen removal.11
- Heterotrophs: These are “BOD removers” that obtain their carbon and energy from organic compounds present in the wastewater. They are responsible for the bulk of organic matter degradation and also play a crucial role in denitrification, where they reduce nitrate to nitrogen gas using organic carbon as an electron donor.11
- Phosphorus Accumulating Organisms (PAOs): These specialized heterotrophic bacteria are central to biological phosphorus removal (BPR). They possess the unique ability to release phosphorus under anaerobic conditions and then rapidly absorb and store excess phosphorus as polyphosphates under aerobic conditions.9
The relative abundance and balance of these microbial populations (autotrophs, heterotrophs, and PAOs) are not static; they are highly influenced by the characteristics of the incoming wastewater, particularly the ratios of chemical oxygen demand (COD), total Kjeldahl nitrogen (TKN), and total phosphorus (TP).12 For instance, the TKN/COD ratio in the primary effluent can significantly determine the populations of autotrophs and ordinary heterotrophs, while the TP/COD ratio primarily influences the PAO population.12 Effective process control therefore involves creating and maintaining environmental conditions that favor the desired microbial groups for specific treatment objectives.
Mean Cell Residence Time (MCRT) / Solids Retention Time (SRT) Management
The Mean Cell Residence Time (MCRT), often interchangeably referred to as Solids Retention Time (SRT) or Cell Residence Time (CRT), is a fundamental operational parameter in activated sludge processes. It quantifies the average amount of time, expressed in days, that the active microbial solids (bacteria) are retained within the entire biological treatment system, encompassing both the aeration tanks and secondary clarifiers.3 Essentially, MCRT is a direct measure of the “age” of the activated sludge.4
The importance of MCRT cannot be overstated, as it is crucial for maintaining a desired microbial population and achieving specific treatment goals.3 For example, nitrification, the biological oxidation of ammonia, requires a relatively long MCRT, typically greater than 4 days, with more stable and complete nitrification often observed at MCRT values exceeding 10 days.3 A higher SRT also leads to a higher rate of endogenous respiration, where microorganisms consume their own cellular material in the absence of external food.11
The calculation of MCRT involves determining the total pounds of mixed liquor suspended solids (MLSS) present in the activated sludge process (aeration tanks plus secondary clarifiers) and dividing that by the total pounds of suspended solids leaving the system per day (including waste activated sludge (WAS) and suspended solids in the final effluent).4 This calculation provides a quantitative measure of how long the active biomass is retained within the system.
Control of MCRT is primarily achieved by adjusting the flow rate of the waste activated sludge (WAS).3 By increasing the WAS rate, the MCRT is shortened, leading to a younger, more active sludge. Conversely, decreasing the WAS rate lengthens the MCRT, resulting in an older, more stable sludge population.
MCRT is arguably the most fundamental operational parameter for activated sludge systems, serving as the master control for biological performance. By controlling the MCRT, operators directly manage the “age” and physiological state of the microbial community. This, in turn, dictates the system’s capacity to perform specific functions, such as nitrification, denitrification, and BOD removal, and significantly influences sludge settleability. It is the primary lever available to operators for steering the biological engine of the plant, ensuring that the microbial population is optimally conditioned for the desired treatment outcomes.
Food-to-Microorganism (F/M) Ratio Control
The Food-to-Microorganism (F/M) ratio is a critical process control parameter that quantifies the amount of organic food (measured as BOD loading) entering the activated sludge process relative to the active microbial biomass (measured as Mixed Liquor Volatile Suspended Solids, MLVSS) present in the aeration tanks.4
Maintaining an optimal F/M ratio is essential for balancing the organic load with the microbial population, thereby ensuring equilibrium and efficient treatment within the system.22 Each activated sludge process configuration typically operates best within a specific range of F/M values.4
- If the F/M ratio is too high, it indicates that there is an excessive amount of food for the available microorganisms. This can lead to insufficient BOD removal and often results in poor sludge settling characteristics.21
- Conversely, if the F/M ratio is too low, it suggests that there is not enough food to sustain vigorous microbial growth. This condition can promote the proliferation of certain filamentous bacteria, leading to sludge bulking, or result in the formation of “pin floc,” which are small, poorly settling particles.14
The calculation of the F/M ratio involves dividing the pounds per day of BOD entering the treatment system by the pounds of MLVSS in the aeration tank.4 The BOD loading in pounds per day is calculated using the formula: Flow (MGD) x BOD concentration (mg/L) x 8.34 lbs/gal.4 Similarly, the pounds of MLVSS in the tank are determined by: Volume (MG) x MLVSS concentration (mg/L) x 8.34 lbs/gal.4
Since the influent BOD cannot be directly controlled by the operator, the F/M ratio is primarily used to determine the desired MLVSS level that needs to be maintained in the aeration tank.22 Operators adjust the MLVSS concentration by manipulating the rates of return activated sludge (RAS) and waste activated sludge (WAS).
Typical F/M ranges vary significantly depending on the activated sludge process configuration:
- Extended aeration systems typically operate at a low F/M ratio of 0.05-0.15.19
- Conventional activated sludge systems generally maintain an F/M ratio between 0.2-0.4.19
- Completely mixed systems often operate in the range of 0.2-0.6.22
- High-rate activated sludge processes can operate at higher F/M ratios, typically 0.4-1.5.22
The F/M ratio serves as a direct indicator of sludge health and settling properties. The explicit correlations between high F/M and poor BOD removal/settling, and low F/M with filamentous bulking and pin floc, demonstrate a clear causal link between this ratio and the physical characteristics of the activated sludge. This makes the F/M ratio an indispensable operational tool for predicting and managing sludge settleability. By diligently maintaining the F/M within its optimal range, operators can proactively prevent common operational problems like bulking or dispersed growth, which are frequent causes of effluent violations. This quantitative parameter provides a robust basis for adjusting RAS and WAS rates to ensure a healthy, active, and well-settling floc.
Dissolved Oxygen (DO) and Aeration Strategies
Importance of DO in Activated Sludge Processes
Dissolved oxygen (DO) is an indispensable component of the activated sludge process, serving as the electron acceptor for the vast majority of aerobic biochemical reactions that drive wastewater treatment.3 These reactions include the crucial reduction of carbonaceous biochemical oxygen demand (BOD) and the biological oxidation of ammonia (nitrification).3
Nitrifying bacteria, being autotrophic, have a specific and critical requirement for dissolved oxygen, typically needing concentrations of 2-3 mg/L to efficiently convert ammonium to nitrate.3 Insufficient DO levels can lead to significant inefficiencies in the nitrification process, resulting in elevated ammonia concentrations in the effluent.5 Furthermore, a low DO environment can dramatically increase the risk of filamentous bacteria development and subsequent sludge bulking, severely impairing sludge settleability and overall plant performance.5 Conversely, denitrification, the process of converting nitrate to nitrogen gas, strictly requires anoxic conditions, meaning very low or no dissolved oxygen, as denitrifying bacteria utilize nitrate as their electron acceptor instead of free oxygen.11 The precise control of DO levels is therefore paramount for achieving both carbonaceous and nitrogenous treatment objectives.
Types of Aeration Systems: Diffused vs. Mechanical
The selection of an aeration system is a critical decision for any wastewater treatment plant, as it directly impacts energy consumption, operational costs, and treatment efficiency. The choice is influenced by factors such as the volume and composition of wastewater, specific oxygen requirements, and the physical dimensions of the treatment tanks or lagoons.23 Broadly, aeration systems are categorized into diffused and mechanical types.
Surface Aerators (Mechanical Systems):
These systems typically employ impellers that operate at or near the water’s surface.
- Characteristics: Horizontal surface aerators, such as brush aerators and paddlewheel aerators, feature a horizontally mounted impeller that rotates close to the water’s surface, drawing liquid and dispersing it radially. This action creates high water velocities and provides efficient aeration over a wide area, making them suitable for shallow basins.24 Vertical surface aerators use vertically oriented impellers that pull water upward and disperse it in a circular pattern. They generally require more depth for effective operation.24
- Advantages: Mechanical surface aerators offer ease of maintenance and can have lower initial capital costs compared to some diffused systems.24 Vertical types provide consistent aeration depth and adaptability to fluctuating water levels in deeper basins.24
- Disadvantages: Mechanical aeration systems generally exhibit lower efficiency in very deep tanks and are more susceptible to harsh weather conditions.23 They tend to have higher energy demands and greater maintenance requirements due to more moving parts.23 Furthermore, surface aerosol formation can lead to unpleasant odors.23
Diffused Aeration Systems:
These systems introduce compressed air into the wastewater through diffusers located near the tank floor.
- Characteristics: Diffused aeration systems typically operate vertically, releasing tiny bubbles from diffusers. Compressed air is pumped through pipes and filters into the water, creating bubbles that displace and mix the water, forming a spiral flow pattern that efficiently transfers oxygen into the water column.23 There are two main types: fine bubble diffusers, known for enhanced aeration and efficiency, and coarse bubble diffusers, which excel at mixing and increasing dissolved oxygen levels.23
- Advantages: Diffused aeration systems are highly regarded for providing uniform mixing and superior energy efficiency, leading to lower long-term operational costs.23 They are durable, with quality systems lasting a decade or more, and offer reliable performance as the diffusers are submerged and less affected by harsh surface conditions.23 They also present a safer working environment as no electrical wires run through the wastewater.23
- Disadvantages: Diffused systems may be less efficient in very shallow tanks, and their diffuser pores can struggle to maintain efficiency under certain conditions.23 Unlike mechanical aerators, diffuser systems are fixed in place, limiting portability.23
Hybrid Systems: Some advanced treatment plants integrate both surface aeration and fine bubble diffusers in hybrid systems to leverage the best features of each approach, thereby achieving enhanced performance and efficiency.24
The selection of an aeration system is a strategic decision with significant long-term implications for operational costs, maintenance burden, and overall treatment efficiency. It is not a one-size-fits-all choice; rather, it depends on a thorough evaluation of specific plant characteristics, such as wastewater volume and composition, tank size, and desired operational goals, including energy efficiency and mixing requirements. Recognizing these trade-offs and aligning the chosen technology with the plant’s unique needs is paramount for sustainable and effective wastewater treatment.
Optimization and Control of Aeration
Optimizing aeration is paramount for both treatment efficacy and energy efficiency, as aeration can account for a substantial portion of a plant’s total energy consumption. Key to successful aeration control is the real-time monitoring of critical parameters, including dissolved oxygen (DO), oxidation-reduction potential (ORP), and nitrate/nitrite concentrations.15
Modern wastewater treatment plants increasingly rely on Supervisory Control and Data Acquisition (SCADA) systems. These systems empower operators to monitor conditions automatically and make rapid process adjustments based on real-time data, significantly enhancing responsiveness and control.7 Advanced control strategies, for instance, can dynamically adjust the aerated volume to maintain desired effluent ammonium levels, even in the face of major changes in influent load.5
The optimization of DO set-points directly contributes to decreased aeration requirements and improved oxygen transfer efficiency, leading to substantial energy savings.7 For example, a new control strategy for simultaneous nitrification-denitrification has demonstrated a remarkable 70% decrease in air requirement while maintaining similar effluent water quality.5 This illustrates the profound impact of precise DO control.
Furthermore, innovations in aerator technology itself contribute to optimization. Modern aerator designs incorporate advanced materials and blade configurations specifically engineered to maximize oxygen transfer while simultaneously minimizing power usage.24 These improved designs, often coupled with automated control systems, provide continuous real-time data monitoring and adjustments, ensuring consistent and efficient aeration that responds dynamically to varying wastewater conditions.24
The increasing reliance on automation in activated sludge operations, particularly for aeration control, signifies a major shift in operational paradigms. Automated systems move beyond manual adjustments to dynamic, data-driven optimization. This is critical for consistently meeting stringent effluent limits while simultaneously reducing energy consumption, which is typically the largest operational cost in wastewater treatment. This trend also implies an evolution in operator skills, requiring a greater emphasis on monitoring, interpreting, and managing automated systems rather than solely focusing on manual control. Automation thus drives both efficiency and stability in advanced wastewater treatment.
Secondary Clarifier Performance

Role and Importance of Secondary Clarifiers
The secondary clarifier, often referred to as the final clarifier, holds a pivotal role in the activated sludge process. Its primary function is to effectively settle the biologically treated solids (activated sludge) that have been produced in the aeration basin, thereby allowing for the discharge of a clear, high-quality effluent.20 Beyond its role in solids-liquid separation, the secondary clarifier also serves as a critical thickening unit. It concentrates the biological solids, enabling a portion to be returned to the aeration tank as Return Activated Sludge (RAS) to maintain the active biomass, while the excess is removed from the system as Waste Activated Sludge (WAS) for further processing.25
The performance of the secondary clarifier is of paramount importance, as it exerts the most significant influence on the overall operational success and effluent quality of the entire wastewater treatment plant.25 Even if the biological processes within the aeration basin are functioning optimally, any failure in the secondary clarifier to effectively separate and thicken the solids can negate all upstream treatment efforts, leading to a loss of solids in the effluent and potential permit violations.20 Thus, the secondary clarifier often acts as the hydraulic and solids separation bottleneck of the activated sludge system.
Performance Metrics: SVI, SOR, SLR, WOR
To effectively monitor and control secondary clarifier performance, several key metrics are routinely employed:
- Sludge Blanket Depth: This refers to the thickness of the layer of settled solids at the bottom of the clarifier.20 Operators typically aim to maintain the sludge blanket between 1 to 3 feet.20 A sludge blanket that is too deep can lead to undesirable denitrification within the clarifier, causing solids to float to the surface and be lost over the weir.20 Sludge blanket depth is commonly measured using a specialized tool like a Sludge Judge®.20
- Sludge Volume Index (SVI): SVI is a numerical expression that quantifies the settling characteristics of activated sludge in the final clarifier.19 It is determined from a 30-minute settleability test, where a 1,000 mL sample of mixed liquor is allowed to settle.19 The SVI is calculated as the volume of settled sludge (in mL/L) divided by the mixed liquor suspended solids (MLSS) concentration (in mg/L), multiplied by 1,000.20 A good settling sludge typically has a textbook SVI value of 100 mL/g, though values between 80 and 150 mL/g are commonly observed in well-operating systems.19 SVI values provide critical indications:
- Less than 100 mL/g: May indicate old biosolids, potential for pin floc, and increasing effluent turbidity.19
- 100 – 250 mL/g: Generally indicates normal operation, good settling, and low effluent turbidity.19
- Greater than 250 mL/g: Points to bulking biosolids, poor settling, and high effluent turbidity.19 High SVI can be caused by filamentous organisms, young/poorly settling sludge, or excessively high MLSS concentrations.20
- Surface Overflow Rate (SOR): Also known as Surface Loading Rate, SOR expresses the relationship between the flow entering the clarifier and its surface area.20 It is typically expressed in gallons per day per square foot (gpd/ft²).20 If the SOR is too high, solids will not have sufficient time to settle and will be discharged with the effluent.20 Conversely, an SOR that is too low can lead to excessively long detention times and septicity within the clarifier.20
- Solids Loading Rate (SLR): SLR quantifies the relationship between the mass of solids entering the clarifier and the clarifier’s surface area.20 It is expressed in pounds per square foot (lbs/ft²).20 If the SLR increases above the design limits, it directly results in an increase in effluent solids.20
- Weir Overflow Rate (WOR): WOR represents the flow in relation to the length of the effluent weir.20 It is expressed in gallons per day per foot (gpd/ft).20 A high WOR can lead to a loss of solids, particularly when the solids settling rate is already poor.20
The secondary clarifier is often the limiting factor for activated sludge plant capacity and effluent quality. Even if the biological processes in the aeration basin are performing optimally, any deficiencies in clarifier performance—whether due to hydraulic overload, poor sludge settling characteristics, or operational issues—can negate all upstream treatment efforts. Such failures directly lead to effluent violations and a compromised treatment outcome. Therefore, operators must prioritize clarifier health and performance as a primary indicator of overall plant stability and regulatory compliance.
Common Clarifier Problems and Optimization Strategies
Secondary clarifiers are susceptible to several common operational problems that can compromise effluent quality and overall plant efficiency.
- Denitrification in Clarifier: As discussed, if the sludge blanket becomes too thick and remains in the clarifier for an extended period, nitrates within the settled sludge can be converted to nitrogen gas by denitrifying bacteria.14 The resulting nitrogen gas bubbles can cause clumps of sludge to become buoyant and float to the surface, leading to solids being lost over the weirs.14 Solutions include minimizing the sludge blanket depth, increasing Return Activated Sludge (RAS) rates to remove sludge faster, and increasing the dissolved oxygen (DO) concentration in the aeration basin, particularly at the clarifier end, to reduce nitrate entering the clarifier or prevent anoxic conditions within it.14
- Hindered Settling: This occurs when the concentration of Mixed Liquor Suspended Solids (MLSS) in the system is excessively high, causing the solids settling in the final clarifier to impede the settling of solids above them.20 This can be observed in 30-minute settling tests, where the settled sludge volume will typically be high (greater than 800 mL/L).20 A diluted settleability test (diluting the mixed liquor sample in half with clear final effluent) can help differentiate hindered settling from excessive filaments; if settling improves with dilution, additional wasting is warranted.20
- Filamentous Organisms: When present in excess, these thread-like microorganisms can severely impair the settling of activated sludge, creating a bulking condition in the final clarifier that leads to poor effluent quality.14
- Solids Washouts: If the flow rate through the final clarifier is too high, solids will not have sufficient time to settle and can be washed out over the weirs.20 This leads to a loss of solids from the system, reducing the amount of active biomass available for return to the aeration basin (RAS) and consequently diminishing overall treatment efficiency, often resulting in effluent permit violations.20
- Short-circuiting: This refers to an uneven flow distribution within a wastewater tank, where density currents cause wastewater to travel faster through certain parts of the tank.20 Short-circuiting is typically more pronounced during periods of high flow.20 To optimize clarifier performance and mitigate short-circuiting, it is crucial to ensure that weirs are level and that flow is evenly distributed to all clarifiers if multiple units are in operation.20 The strategic placement of baffles within the clarifier can also help to improve flow patterns, especially during high flow periods.20
Optimization strategies for final clarifier performance are multifaceted and require a holistic approach:
- Mixed Liquor Settleability: The foundation of good clarifier performance lies in optimizing the settleability of the mixed liquor. This is achieved by maintaining proper environmental conditions in the aeration basin that favor the growth and health of robust, large floc-forming bacteria, rather than filamentous organisms, through consistent process control.20
- Clarifier Optimization: Beyond flow distribution and baffles, setting Return Activated Sludge (RAS) rates appropriately to minimize sludge blanket depth (ideally less than a foot) is critical.20
- Reduce Clarifier Solids Loading: The Solids Loading Rate (SLR) on the clarifier is influenced by both incoming flow and RAS flowrate. Strategies to reduce solids loading include bringing any extra, unused tankages (e.g., another clarifier or aeration basin) online if available, or temporarily taking some aeration basins offline to store solids until flows subside.20 Operating the aeration basins in a step-feed configuration can also reduce the solids concentration at the end of the aeration basins, thereby decreasing the solids load entering the final clarifier.20 Adjusting the RAS rate to balance the lowest possible sludge blanket at the lowest SLR is also beneficial.20
- Addressing Hydraulic Overloads: The ability of activated sludge systems to handle peak flows is primarily limited by solids separation in the clarifier.20 The most effective long-term strategy for maintaining consistent wastewater treatment during wet weather events is to reduce the amount of inflow and infiltration (I/I) of clear water entering the sewer system through ongoing collection system Capacity, Management, Operation, and Maintenance (CMOM) programs.20
Effective clarifier management necessitates a holistic understanding of the entire wastewater treatment system. Clarifier problems are frequently symptoms of issues originating upstream—such as imbalances in sludge age, an unhealthy microbial community in the aeration basin, or external factors like excessive hydraulic loading from inflow and infiltration.6 Therefore, operators cannot focus on the clarifier in isolation. They must comprehend how influent characteristics, aeration basin dynamics, and overall sludge management practices collectively impact clarifier performance. This integrated, plant-wide perspective is essential for accurate troubleshooting and sustained optimization, ensuring that the clarifier functions efficiently as the final barrier for effluent quality.
Table 4: Secondary Clarifier Performance Metrics and Troubleshooting
This table consolidates key performance indicators for secondary clarifiers, providing both quantitative targets and qualitative observations. By linking each metric to potential problems, their causes, and recommended solutions, it empowers operators to quickly diagnose and respond to clarifier upsets, which are often the most visible and impactful issues affecting effluent quality.
Metric | Definition/Significance | Typical/Optimal Range | Common Problem(s) Associated with Deviations | Potential Cause(s) | Recommended Operational Adjustment(s) |
Sludge Blanket Depth | Thickness of settled solids layer at bottom of clarifier. Indicates solids inventory. | 1 to 3 feet 20 | Too deep: Denitrification, solids floating (ashing), solids loss over weir 20 | High solids loading, insufficient RAS rate, poor settling sludge, septicity 20 | Increase RAS rate; increase WAS rate; ensure proper DO in aeration basin end; improve sludge settleability.14 |
Sludge Volume Index (SVI) | Numerical expression of sludge settling characteristics. | 80 – 150 mL/g (good settling) 20 | <100 mL/g: Old biosolids, pin floc, increasing turbidity 19 | Low F/M, chronic toxicity, excessive wasting 14 | Adjust MCRT (increase F/M); check for toxicity; reduce wasting if too low.6 |
>250 mL/g: Bulking biosolids, poor settling, high turbidity 19 | Filamentous organisms, young sludge, too high MLSS 19 | Identify/address filament cause (DO, nutrients, F/M, septicity); adjust MCRT; optimize MLSS.6 | |||
Surface Overflow Rate (SOR) | Flow into clarifier per unit surface area. | Varies by design (e.g., 400-800 gpd/ft²) 20 | Too high: Solids discharge with effluent 20 | Hydraulic overload, high influent flow, insufficient clarifier capacity 20 | Reduce influent flow (I/I control); bring additional clarifiers online; implement flow equalization.20 |
Too low: Long detention time, septicity 20 | Low flow, excessive clarifier capacity in use 20 | Take clarifiers offline; optimize flow distribution. | |||
Solids Loading Rate (SLR) | Mass of solids entering clarifier per unit surface area. | Varies by design (e.g., 15-30 lbs/day/ft²) 20 | Increases above design limits: Increase in effluent solids 20 | High MLSS, high influent flow, poor sludge settleability 20 | Reduce MLSS; reduce influent flow; improve sludge settleability; use step feed.20 |
Weir Overflow Rate (WOR) | Flow over effluent weir per unit weir length. | Varies by design (e.g., 10,000-20,000 gpd/ft) 20 | High WOR: Loss of solids, especially with poor settling 20 | High influent flow, uneven weir levels, insufficient weir length 20 | Ensure weirs are level; optimize flow distribution; consider adding weir length or baffles.20 |
This table is indispensable for operators preparing for the certification exam and for daily operational management. It centralizes key performance indicators for secondary clarifiers, providing both quantitative targets and qualitative observations. By linking each metric to potential problems, their causes, and recommended solutions, it empowers operators to quickly diagnose and respond to clarifier upsets, which are often the most visible and impactful issues affecting effluent quality. This systematic approach enhances troubleshooting efficiency and prevents minor issues from escalating into major compliance failures, thereby ensuring consistent and reliable plant performance.
MLSS/MLVSS Monitoring and Interpretation
Definitions and Significance of MLSS and MLVSS
Accurate monitoring and interpretation of Mixed Liquor Suspended Solids (MLSS) and Mixed Liquor Volatile Suspended Solids (MLVSS) are foundational to effective activated sludge process control. These parameters provide critical insights into the quantity and activity of the biomass within the aeration tank.
- Mixed Liquor Suspended Solids (MLSS): MLSS represents the total concentration of all suspended solids present in the aeration tank, typically measured in milligrams per liter (mg/L).19 This heterogeneous mixture comprises the incoming wastewater solids combined with the active biomass (microorganisms) returned from the secondary clarifier as Return Activated Sludge (RAS).21 The measurement of MLSS involves filtering a sample through a 0.45-micron filter, followed by drying and weighing the retained solids.21 MLSS provides an overall measure of the solids inventory in the aeration basin.
- Mixed Liquor Volatile Suspended Solids (MLVSS): MLVSS represents the volatile portion of the MLSS, typically constituting around 70% of the total MLSS.21 Crucially, MLVSS is considered the best indicator of the concentration of active microorganisms (bacteria) available to consume wastes and perform the desired biological treatment.4 The volatile solids are determined by heating the filtered MLSS solids in a muffle furnace to 550°C; the weight loss upon ignition represents the volatile (organic) portion, which is primarily the microbial biomass.4
The significance of MLVSS lies in its direct correlation to the active biomass, which is essentially the “engine” of the activated sludge process. Its concentration is a critical input for calculating other key process control parameters, such as the Food-to-Microorganism (F/M) ratio and the Mean Cell Residence Time (MCRT).4 Therefore, understanding and managing MLVSS levels are paramount for optimizing treatment efficiency.
Practical Monitoring and Interpretation for Process Control
Regular and accurate measurement of MLSS and MLVSS concentrations is fundamental for controlling the amount of solids under aeration and making informed operational decisions.19 A widely used calculation method for converting concentrations to mass (pounds) in wastewater treatment is the “pounds formula”: Pounds = Flow (MGD) x Concentration (mg/L) x 8.34 lbs/gal.19 This versatile formula is applied across various calculations, including:
- Calculating the BOD loading entering the aeration basin.19
- Determining the total pounds of MLSS or MLVSS present in the aeration basin.19
- Quantifying the mass of solids leaving the system via waste activated sludge (WAS) or in the final effluent.19
For example, to calculate the pounds of MLSS in an aeration basin, the formula would be: MLSS (lbs) = MLSS (mg/L) x Volume (MG) x 8.34 lbs/gal.19
MLSS/MLVSS monitoring is not merely a routine laboratory test; it provides the essential quantitative data that forms the bedrock for all major activated sludge process control decisions. Without accurate and timely MLSS/MLVSS data, operators would be unable to precisely calculate or adjust critical parameters such as the F/M ratio, MCRT, or RAS/WAS rates. This lack of quantitative basis would lead to inefficient, unstable, and potentially non-compliant operations. Therefore, these measurements are indispensable for data-driven process management, enabling operators to maintain the optimal balance between food and microorganisms and to manage the age of the sludge effectively.
Table 5: Key Activated Sludge Calculations and Formulas
This table centralizes the most frequently used calculations in activated sludge process control, providing clear formulas, definitions, and practical examples. The ability to perform these calculations is a core competency for Grade IV operators, as indicated by the “Calculation Items” in the exam outline.1
Calculation Type | Formula | Definition of Terms/Variables | Example Calculation | Typical Range/Significance |
Pounds of BOD per Day | Lbs/Day = Flow (MGD) x Conc (mg/L) x 8.34 lbs/gal 19 | Flow: Million Gallons per Day (MGD); Conc: BOD concentration (mg/L); 8.34: conversion factor (lbs/gal) | Calculate BOD entering aeration tank: Flow = 2.0 MGD, BOD Conc = 260 mg/L. Lbs/Day = 2.0 MGD x 260 mg/L x 8.34 lbs/gal = 4,336.8 lbs/day 21 | Represents the “food” load on the system. |
Pounds of MLSS in Aeration Tank | MLSS, lb = MLSS, mg/L x Volume, MG x 8.34 lb/gal 19 | MLSS: Mixed Liquor Suspended Solids (mg/L); Volume: Aeration tank volume (MG) | Calculate MLSS in aeration tank: Volume = 0.35 MG, MLSS = 2,200 mg/L. Lbs = 0.35 MG x 2,200 mg/L x 8.34 lb/gal = 6,422 lbs 19 | Total solids in the aeration tank. |
Pounds of MLVSS in Aeration Tank | Lbs MLVSS = Volume (MG) x MLVSS (mg/L) x 8.34 lbs/gal 21 | MLVSS: Mixed Liquor Volatile Suspended Solids (mg/L); Volume: Aeration tank volume (MG) | Calculate MLVSS in aeration tank: MLSS = 2,060 mg/L, Volatile solids = 70%, Volume = 1.5 MG. MLVSS Conc = 2,060 x 0.7 = 1,442 mg/L. Lbs MLVSS = 1.5 MG x 1,442 mg/L x 8.34 lbs/gal = 18,039.4 lbs 21 | Represents the active microbial biomass. |
Food-to-Microorganism (F/M) Ratio | F:M = (Lbs/day BOD entering treatment) / (Lbs MLVSS in aeration tank) 4 | Lbs/day BOD: Calculated above; Lbs MLVSS: Calculated above | Determine MLVSS for desired F:M: BOD = 630 lbs/day, Volume = 0.105 MG, Desired F:M = 0.3. Lbs MLVSS = 630 / 0.3 = 2,100 lbs. Conc (mg/L) = 2,100 lbs / (0.105 MG x 8.34 lbs/gal) = 2,398.08 mg/L 21 | Conventional: 0.2-0.4; Extended Aeration: 0.05-0.15.19 Balances food with microbes. |
Mean Cell Residence Time (MCRT) | MCRT = (Pounds of MLSS under aeration) / (Lbs/day suspended solids leaving system) 4 | Lbs MLSS under aeration: Total MLSS in aeration tanks + clarifiers; Lbs/day leaving: (WAS in lbs/day) + (Effluent SS in lbs/day) 4 | Calculate MCRT: Total MLSS = 21,371.25 lbs; WAS = 3,660.4 lbs/day; Effluent SS = 574.6 lbs/day. MCRT = 21,371.25 / (3,660.4 + 574.6) = 5.05 days 21 | Nitrification: >4 days, often >10 days.3 Average time bacteria remain in system. |
Return Activated Sludge (RAS) Flow Rate | RAS flow rate = Q x22 | Q: Influent flow rate (MGD or m3/day); MLSS: Mixed Liquor Suspended Solids (mg/L); RAS SS: Suspended solids in return activated sludge (mg/L) | Calculate RAS flow rate: Q = 5,000 m3/day, MLSS = 650 mg/L, RAS SS = 7,000 mg/L. RAS flow rate = 5,000 x [650 / (7,000 – 650)] = 511 m3/day 22 | Commonly 30-125% of influent flow.21 Recycles active biomass. |
This table is invaluable for both exam preparation and daily operational duties. It centralizes the most frequently used calculations in activated sludge process control, providing clear formulas and practical examples. The ability to perform these calculations—for instance, determining the required MLVSS for a target F/M ratio or calculating the Mean Cell Residence Time—is a core competency for Grade IV operators, as directly indicated by the “Calculation Items” section in the exam outline.1 By presenting this information concisely and with illustrative examples, it serves as a quick reference, significantly reducing the cognitive load on operators and enabling them to focus on interpreting the results for precise process adjustments.
RAS/WAS Optimization and Impacts
Return Activated Sludge (RAS): Role and Control
Return Activated Sludge (RAS) is a cornerstone of the activated sludge process, involving the continuous recirculation of a portion of the settled active biomass from the secondary clarifier back to the aeration tank.3 The fundamental role of RAS is to ensure a consistent and adequate supply of active microorganisms in the aeration basin. This continuous reintroduction of “hungry” microbes is essential for efficiently breaking down pollutants and maintaining the delicate biological balance necessary for optimal wastewater treatment.26
The RAS flow rate is a critical control parameter that operators must meticulously manage.22 Adjustments to the RAS rate are typically made based on prevailing influent conditions, the desired sludge age (MCRT), and the need to maintain a consistent and optimal sludge blanket depth within the secondary clarifier.25 Operators use pumps or valves to increase or decrease the return rate, thereby controlling the concentration of activated sludge in the aeration tank and the clarifier.26 Commonly, RAS flow rates range from 30% to approximately 125% of the influent flow.21 The RAS flow rate can be calculated using the formula: RAS flow rate = Q x, where Q is the influent flow rate, MLSS is the mixed liquor suspended solids concentration, and RAS SS is the suspended solids concentration in the return activated sludge.22
The concentration and flow rate of RAS have direct and significant impacts on treatment performance:
- Capacity to Process Waste: The RAS concentration directly affects the system’s capacity to process incoming organic waste.26 If the RAS concentration is too low, there may be insufficient active microorganisms in the aeration tank to effectively break down organic materials, leading to poor treatment performance and compromised effluent quality.26
- Sludge Buildup and Oxygen Demand: Conversely, if the RAS concentration is too high, it can lead to excessive sludge buildup in the clarifier, which can increase oxygen demand within the clarifier (potentially leading to denitrification) and even cause system clogging.26
- Sludge Age and System Stability: The recycling process facilitated by RAS helps to control the sludge age (MCRT) and supports the overall stability of the treatment system.26 A stable system is better equipped to treat variable loads of wastewater effectively.
Operational challenges associated with RAS include potential blockages in return lines, difficulties in maintenance, and the constant need to balance flow rates to optimize efficiency.26
RAS serves as the primary hydraulic link for solids management within the activated sludge system. It physically transports the active biomass (microorganisms) from the secondary clarifier back to the aeration basin. This direct hydraulic control directly impacts the Mixed Liquor Suspended Solids (MLSS) concentration in the aeration tank and, consequently, the sludge blanket depth in the clarifier.25 Therefore, its optimization is crucial for maintaining the desired MLSS concentration, preventing clarifier washout, and ensuring an adequate microbial population for effective treatment. Incorrect RAS rates can rapidly lead to both biological imbalances (e.g., insufficient BOD removal) and physical upsets (e.g., clarifier overflow), highlighting its immediate and tangible impact on daily operations and effluent quality.
Waste Activated Sludge (WAS): Management and Impacts
Waste Activated Sludge (WAS) refers to the process of removing excess biomass from the activated sludge system. Microorganisms in the aeration tank reproduce rapidly as they consume organic matter.3 If this excess biomass is not regularly removed, the system can become overpopulated, leading to starvation of the microbes and a decline in treatment efficiency.3 Therefore, WAS is essential for maintaining a desired microbial population for effective process control.3
The management of WAS directly controls the Mean Cell Residence Time (MCRT), also known as sludge age.3 By adjusting the WAS flow rate, operators can dictate how long the active biomass remains in the system. Regular monitoring of sludge characteristics helps determine the appropriate time and rate for removing excess sludge to optimize treatment efficiency.26
The impacts of WAS management are far-reaching:
- Microbial Community Structure and Treatment Objectives: WAS directly influences the sludge age, which in turn dictates the microbial community structure and its ability to achieve specific treatment objectives.3 For instance, a longer sludge age (lower WAS rate) is typically required for nitrification, while a shorter sludge age (higher WAS rate) might be favored for high-rate BOD removal.
- Sludge Volume: In biological nutrient removal (BNR) systems, increased phosphorus removal, in particular, leads to higher volumes of excess sludge because PAOs accumulate phosphorus within their cells.8 This necessitates efficient and sustainable disposal strategies for the generated sludge.8
- Treatment Efficiency: Deviations from the optimal sludge age due to improper WAS management can result in inadequate treatment performance or other operational inefficiencies.26
WAS serves as the fundamental biological regulator of sludge age. By adjusting the rate at which excess biomass is removed, operators can directly control the “age” and physiological state of the activated sludge. This allows for the selection and enrichment of desired microbial populations (e.g., slower-growing nitrifiers requiring longer MCRT) and prevents the accumulation of old, less active sludge or the washout of young, poorly settling sludge. The decisions made regarding WAS rates have cascading effects on the overall treatment efficiency, sludge settleability, and the operational burden and costs associated with downstream solids handling processes.
Optimization of RAS/WAS for System Stability and Effluent Quality
The effective optimization of both Return Activated Sludge (RAS) and Waste Activated Sludge (WAS) is paramount for ensuring the overall stability of the activated sludge treatment system and consistently achieving high effluent quality.26 While RAS and WAS are distinct control points—RAS being a hydraulic return for biomass, and WAS being a biological removal mechanism for excess sludge—their effective management is inherently interdependent and crucial for maintaining system balance.
For instance, excessive wasting (high WAS) without adequate return (low RAS) can deplete the active biomass in the aeration basin, leading to insufficient treatment. Conversely, a high RAS rate without sufficient wasting can lead to an accumulation of old, less active sludge, potentially causing poor settling characteristics and clarifier upsets. True optimization involves a coordinated strategy for both RAS and WAS, ensuring that the right quantity of active biomass is maintained in the aeration basin to meet the incoming organic and nutrient loads, while simultaneously preventing excessive solids accumulation in the clarifier and managing the overall sludge inventory efficiently.
To achieve this balance, operators can employ several strategies:
- Adjusting Aeration Rates: Optimizing aeration rates in conjunction with RAS/WAS adjustments helps maintain optimal dissolved oxygen levels, which in turn influences microbial activity and sludge settleability.26
- Real-time Data Collection: Implementing real-time data collection for parameters like MLSS, MLVSS, DO, and nutrient concentrations allows for dynamic adjustments to RAS and WAS rates, optimizing sludge age and improving nutrient removal efficiency in response to changing influent conditions.26
- Effective Mixing Techniques: Ensuring proper mixing within the aeration tanks prevents sludge settling in undesirable zones and reduces the risk of blockages, contributing to overall system stability.26
The interdependence of RAS and WAS for system balance highlights that these are two sides of the same coin when managing the activated sludge biomass. Operators must possess a comprehensive understanding of their combined impact on MLSS concentration, sludge age, and clarifier performance. Coordinated management of both parameters is essential for achieving efficient waste removal, maintaining a stable treatment system that can effectively handle variable loads, and consistently meeting regulatory compliance standards. This integrated approach to process control is a hallmark of advanced wastewater treatment operations.
The 100-Question Multiple Choice Quiz
This section contains a 100-question multiple-choice quiz designed to prepare candidates for the Grade IV ABC/WPI Wastewater Certification Exam, with a specific focus on advanced activated sludge processes. The questions cover a range of difficulty levels, from basic concept checks to in-depth scenario-based troubleshooting, and include calculations. Each question has four answer choices (A-D), with only one correct answer indicated.
Grade IV ABC/WPI Wastewater Certification Exam Preparation Quiz: Advanced Activated Sludge Processes
Instructions: Choose the best answer for each question.
Biological Nutrient Removal (BNR)
- What is the primary purpose of Biological Nutrient Removal (BNR) in wastewater treatment?A. To remove heavy metals from industrial wastewater.B. To reduce excess nitrogen and phosphorus to prevent eutrophication.C. To disinfect wastewater using biological agents.D. To remove suspended solids through physical filtration.Correct Answer: B
- Which of the following is a key advantage of BNR systems compared to conventional wastewater treatment methods?A. Lower initial capital costs.B. Reduced complexity in operations.C. Superior nutrient removal efficiency.D. Less sludge generation.Correct Answer: C
- In a typical BNR system, what are the two main environmental conditions employed sequentially?A. High temperature and low pH.B. Anaerobic and aerobic conditions.C. High pressure and vacuum.D. High alkalinity and low salinity.Correct Answer: B
- During the anaerobic phase of BNR, what is the primary metabolic activity of Phosphorus Accumulating Organisms (PAOs)?A. Oxidation of ammonia to nitrate.B. Reduction of nitrate to nitrogen gas.C. Release of stored phosphorus and uptake of volatile fatty acids.D. Consumption of dissolved oxygen for organic matter degradation.Correct Answer: C
- What is the main fate of phosphorus that is removed biologically in a BNR system?A. It is converted into soluble forms and discharged with the effluent.B. It is released as gaseous phosphorus into the atmosphere.C. It is incorporated into cell biomass and removed via sludge wasting.D. It is chemically precipitated and recycled back to the anaerobic zone.Correct Answer: C
- According to a 2020 analysis, BNR systems can remove up to what percentage of nitrogen from municipal wastewater?A. 50%B. 65%C. 80%D. 90%Correct Answer: D
- Which of the following is a significant challenge associated with the operation of BNR systems?A. Simplicity in process control.B. Minimal sludge generation.C. Meticulous control over operating conditions like temperature and pH.D. Low initial capital investment.Correct Answer: C
- How do BNR systems generally impact the volume of excess sludge generated compared to conventional treatment methods?A. They significantly reduce sludge volume.B. They have no impact on sludge volume.C. They lead to higher sludge volumes due to increased phosphorus removal.D. They convert all sludge into a reusable byproduct.Correct Answer: C
- What is a key long-term operational benefit of implementing BNR technology, despite potentially higher initial capital costs?A. Increased need for expensive downstream chemical treatments.B. Substantial reduction in nutrient discharge, leading to regulatory non-compliance.C. Enhanced nutrient removal reduces the need for expensive downstream treatments.D. Higher energy consumption due to complex processes.Correct Answer: C
- In a BNR system, what is the primary role of the aerobic phase concerning phosphorus removal?A. PAOs release phosphorus into the soluble form.B. PAOs utilize stored carbon to absorb and store orthophosphates.C. Nitrogen is converted into nitrogen gas.D. Volatile fatty acids are produced.Correct Answer: B
Nitrification and Denitrification
- What is the first step in the nitrification process?A. Oxidation of nitrite-nitrogen to nitrate-nitrogen.B. Reduction of nitrate to nitrogen gas.C. Oxidation of ammonia to nitrite-nitrogen.D. Conversion of organic nitrogen to ammonia.Correct Answer: C
- Which group of bacteria is primarily responsible for the oxidation of ammonia to nitrite?A. NitrobacterB. DenitrifiersC. NitrosomonasD. Phosphorus Accumulating Organisms (PAOs)Correct Answer: C
- Nitrifying bacteria are classified as:A. HeterotrophicB. AutotrophicC. AnaerobicD. FacultativeCorrect Answer: B
- What is the optimal dissolved oxygen (DO) range for effective nitrification in an activated sludge system?A. 0-0.5 mg/LB. 1.0-1.5 mg/LC. 2-3 mg/LD. Above 5 mg/LCorrect Answer: C
- What is a significant consequence of extensive nitrification on wastewater alkalinity?A. It significantly increases alkalinity.B. It consumes alkalinity, potentially lowering pH.C. It has no effect on alkalinity.D. It converts alkalinity into nitrogen gas.Correct Answer: B
- Which of the following is the final product of complete denitrification?A. Ammonia (NH3)B. Nitrite (NO2-)C. Nitrate (NO3-)D. Nitrogen gas (N2)Correct Answer: D
- Denitrification primarily occurs under what environmental conditions?A. Aerobic (high DO)B. Anaerobic (no DO, no nitrate)C. Anoxic (low or no DO, with nitrate)D. High pH and high temperatureCorrect Answer: C
- Denitrifying bacteria are typically classified as:A. AutotrophicB. ChemosyntheticC. HeterotrophicD. PhotosyntheticCorrect Answer: C
- Why is an organic carbon source essential for the denitrification process?A. It provides oxygen for the bacteria.B. It acts as an electron donor for nitrate reduction.C. It increases the pH of the wastewater.D. It inhibits the growth of nitrifying bacteria.Correct Answer: B
- What is a key benefit of denitrification beyond nitrogen removal?A. It increases oxygen demand in the aeration basin.B. It consumes alkalinity, lowering pH.C. It produces alkalinity and recovers oxygen.D. It promotes filamentous bulking.Correct Answer: C
- An operator observes a sudden drop in pH in the aeration basin, accompanied by a decline in nitrification efficiency. What is the most probable cause?A. Excessive denitrification.B. Insufficient aeration leading to high DO.C. Alkalinity consumption due to extensive nitrification.D. High influent BOD load.Correct Answer: C
- What is the typical MCRT (Mean Cell Residence Time) range required for stable nitrification in an activated sludge system?A. Less than 2 days.B. 2-4 days.C. Greater than 4 days, often >10 days.D. No specific MCRT requirement.Correct Answer: C
- Which of the following is an effective strategy to address low effluent pH caused by nitrification?A. Increase aeration rates significantly.B. Decrease the MCRT to inhibit nitrifiers.C. Add chemical alkalinity (e.g., lime or soda ash).D. Increase the influent C/N ratio.Correct Answer: C
- If the COD level in the waste is too low, what operational adjustment can be made to improve denitrification efficiency?A. Increase aeration in the anoxic zone.B. Add an external carbon source like methanol or acetic acid.C. Increase the sludge wasting rate.D. Decrease the internal recycle flow.Correct Answer: B
- An operator notices sludge rising to the surface in the final clarifier, forming clumps. A settling test shows sludge “popping” within 2 hours. What is the likely cause?A. Hydraulic overload.B. Denitrification occurring in the clarifier.C. Excessive old sludge.D. Low DO bulking.Correct Answer: B
Advanced Process Configurations (Bardenpho, A2/O, MLE)
- Which advanced activated sludge process configuration is characterized by an anoxic tank followed by an aerobic tank with an internal recycle from aerobic to anoxic?A. Modified Bardenpho process.B. Anaerobic/Anoxic/Aerobic (A2/O) process.C. Modified Ludzack-Ettinger (MLE) process.D. Oxidation Ditch.Correct Answer: C
- The primary purpose of the internal recycle in the MLE process is to:A. Return phosphorus-rich sludge to the anaerobic zone.B. Recycle nitrate from the aerobic zone to the anoxic zone for denitrification.C. Increase the dissolved oxygen concentration in the anoxic zone.D. Reduce the hydraulic residence time in the system.Correct Answer: B
- A key benefit of optimizing the Internal Recycle Flow (IRQ) set-point in an MLE process is:A. Increasing effluent total nitrogen.B. Maximizing aeration requirements.C. Maximizing oxygen credits generated in the anoxic zone.D. Promoting sludge bulking.Correct Answer: C
- What is the typical range for Internal Recycle Flow (IRQ) rates in an MLE process, as a percentage of the process influent flow rate?A. 50-100%B. 100-200%C. 200-400%D. 400-600%Correct Answer: C
- The A2/O (Anaerobic/Anoxic/Aerobic) process is primarily designed for the removal of:A. Only organic matter.B. Only suspended solids.C. Nitrogen and phosphorus.D. Heavy metals and pathogens.Correct Answer: C
- In the A2/O process, which tank is characterized by the absence of dissolved oxygen and nitrates, where PAOs release phosphorus?A. Aerobic Tank.B. Anoxic Tank.C. Anaerobic Tank.D. Secondary Clarifier.Correct Answer: C
- Which microbial group is primarily active in the aerobic tank of the A2/O process for nitrogen removal?A. Denitrifying microorganisms.B. Phosphorus Accumulating Organisms (PAOs).C. Nitrifying bacteria (Nitrosomonas, Nitrobacter).D. Sulfate-reducing bacteria.Correct Answer: C
- What is the typical Sludge Retention Time (SRT) range for the A2/O process?A. 1-4 days.B. 5-25 days.C. 30-50 days.D. Over 60 days.Correct Answer: B
- The Modified Bardenpho process consists of how many distinct reactor stages?A. Three.B. Four.C. Five.D. Six.Correct Answer: C
- What is the sequence of reactors in the Modified Bardenpho process?A. Aerobic, Anoxic, Anaerobic, Second Anoxic, Second Aerobic.B. Anaerobic, First Anoxic, First Aerobic, Second Anoxic, Second Aerobic.C. Anoxic, Anaerobic, Aerobic, Second Aerobic, Second Anoxic.D. Anaerobic, Aerobic, Anoxic, Second Aerobic, Second Anoxic.Correct Answer: B
- In the Modified Bardenpho process, where does the internal recycle (IR) line typically return nitrate from?A. From the secondary clarifier to the anaerobic reactor.B. From the second aerobic reactor to the first anoxic reactor.C. From the first aerobic reactor to the first anoxic reactor.D. From the anaerobic reactor to the second aerobic reactor.Correct Answer: C
- A significant advantage of the Modified Bardenpho process, beyond N and P removal, is its ability to reduce:A. Only BOD and TSS.B. Only heavy metals.C. COD, BOD, TSS, heavy metals, and viruses.D. Only salinity.Correct Answer: C
- Which of the following is an economic benefit of the Modified Bardenpho process compared to conventional biological methods?A. Increased chemical consumption.B. Higher excess sludge volumes.C. Reduced energy consumption due to anaerobic/anoxic zones.D. Higher initial capital costs with no long-term savings.Correct Answer: C
- An operator is troubleshooting an A2/O plant experiencing poor phosphorus removal. Which zone should be investigated for sufficient volatile fatty acids (VFAs) availability?A. Aerobic tank.B. Anoxic tank.C. Anaerobic tank.D. Secondary clarifier.Correct Answer: C
- An MLE plant operator observes high nitrate in the effluent despite adequate aeration. What is a likely operational issue?A. Insufficient dissolved oxygen in the aerobic zone.B. Excessively high internal recycle rate.C. Insufficient carbon source for denitrification in the anoxic zone.D. Too high sludge wasting rate.Correct Answer: C
Microbiology and Sludge Age Management
- Which of the following is a key microbial population found in the activated sludge aeration basin?A. Pathogenic viruses only.B. Flocculated bacteria, fungi, protozoa, and rotifers.C. Algae and cyanobacteria.D. Only nitrifying bacteria.Correct Answer: B
- What does MLVSS (Mixed Liquor Volatile Suspended Solids) primarily represent in the activated sludge process?A. Total inorganic suspended solids.B. Non-biodegradable suspended matter.C. The concentration of active microorganisms.D. Dissolved organic compounds.Correct Answer: C
- The Mean Cell Residence Time (MCRT) is also known by what other common term?A. Hydraulic Residence Time (HRT).B. Food-to-Microorganism (F/M) Ratio.C. Sludge Retention Time (SRT).D. Sludge Volume Index (SVI).Correct Answer: C
- What is the primary method for controlling the Mean Cell Residence Time (MCRT) in an activated sludge system?A. Adjusting the influent flow rate.B. Controlling the dissolved oxygen concentration.C. Adjusting the Waste Activated Sludge (WAS) flow rate.D. Changing the aeration tank volume.Correct Answer: C
- A longer MCRT in an activated sludge system generally favors the growth of which type of bacteria?A. Fast-growing heterotrophs.B. Filamentous bacteria causing bulking.C. Slower-growing nitrifying bacteria.D. Denitrifying bacteria.Correct Answer: C
- What does the Food-to-Microorganism (F/M) ratio measure?A. The ratio of oxygen consumed to biomass produced.B. The ratio of influent BOD loading to the MLVSS in the aeration tanks.C. The ratio of total suspended solids to volatile suspended solids.D. The ratio of return activated sludge to waste activated sludge.Correct Answer: B
- If the F/M ratio in an activated sludge system is too high, what is a likely consequence?A. Enhanced nitrification.B. Improved sludge settling.C. Insufficient BOD removal and poor settling.D. Promotion of filamentous bacteria.Correct Answer: C
- A low F/M ratio can lead to which of the following problems?A. Increased BOD removal efficiency.B. Promotion of filamentous bacteria and pin floc.C. Reduced sludge volume.D. Higher dissolved oxygen demand.Correct Answer: B
- For a conventional activated sludge process, what is a typical optimal F/M ratio range?A. 0.05 – 0.15B. 0.2 – 0.4C. 0.4 – 0.6D. 0.8 – 1.5Correct Answer: B
- An operator increases the sludge wasting rate. What immediate effect would this have on the MCRT?A. Increase the MCRT.B. Decrease the MCRT.C. Have no effect on MCRT.D. Increase the F/M ratio.Correct Answer: B
Dissolved Oxygen (DO) and Aeration Strategies
- What is the primary role of dissolved oxygen (DO) in the aerobic zone of an activated sludge process?A. To inhibit microbial growth.B. To serve as an electron acceptor for aerobic biochemical reactions.C. To strip nitrogen gas from the wastewater.D. To chemically precipitate phosphorus.Correct Answer: B
- Low dissolved oxygen (DO) levels in the aeration basin can lead to which of the following problems?A. Enhanced nitrification.B. Increased risk of filamentous bacteria development and sludge bulking.C. Reduced energy consumption for aeration without negative impact.D. Improved sludge settling characteristics.Correct Answer: B
- Which type of aeration system typically releases fine or coarse bubbles from diffusers located near the tank floor?A. Surface aerators.B. Mechanical aerators.C. Diffused aeration systems.D. Paddlewheel aerators.Correct Answer: C
- What is a key advantage of diffused aeration systems compared to mechanical surface aerators?A. Easier maintenance.B. Lower initial costs.C. Higher energy efficiency and lower long-term costs.D. Better performance in very shallow tanks.Correct Answer: C
- Which of the following is a disadvantage of mechanical surface aerators?A. Lack of portability.B. Lower efficiency in very deep tanks.C. Higher durability and longevity.D. Safer working environment due to no electrical wires in wastewater.Correct Answer: B
- What is the purpose of real-time monitoring of parameters like DO, ORP, and nitrate/nitrite concentrations in activated sludge process control?A. To increase chemical consumption.B. To allow operators to make slower process adjustments.C. To enable automatic monitoring and faster process adjustments.D. To reduce the need for operator training.Correct Answer: C
- A SCADA (Supervisory Control and Data Acquisition) system in a wastewater treatment plant primarily aids in:A. Manual operation only.B. Real-time data monitoring and automated process adjustments.C. Laboratory analysis of samples.D. Physical removal of sludge.Correct Answer: B
- What is a significant benefit of optimizing dissolved oxygen (DO) set-points in an aeration system?A. Increased aeration requirements.B. Decreased oxygen transfer efficiency.C. Significant energy savings.D. Promotion of anaerobic conditions.Correct Answer: C
- Modern aerator designs often incorporate advanced materials and blade configurations to achieve what primary goal?A. To increase noise pollution.B. To maximize oxygen transfer while minimizing power usage.C. To reduce the lifespan of the equipment.D. To increase maintenance requirements.Correct Answer: B
- An operator observes a persistent filamentous bulking issue in the aeration basin. Lab tests confirm the presence of Sphaerotilus natans. What is the most likely operational parameter to adjust?A. Decrease the F/M ratio.B. Increase the dissolved oxygen (DO) concentration.C. Increase the RAS rate.D. Decrease the sludge wasting rate.Correct Answer: B
Secondary Clarifier Performance
- What is the primary purpose of a secondary (final) clarifier in the activated sludge process?A. To remove grit and large debris.B. To settle secondary biological treatment solids and discharge clear effluent.C. To provide anaerobic conditions for phosphorus release.D. To introduce oxygen for nitrification.Correct Answer: B
- Beyond solids separation, what other crucial function does a secondary clarifier perform?A. Aeration of the mixed liquor.B. Disinfection of the effluent.C. Thickening of biological solids for return or wasting.D. Chemical precipitation of nutrients.Correct Answer: C
- What is the typical desired range for sludge blanket depth in a secondary clarifier?A. 0-6 inches.B. 1 to 3 feet.C. 5 to 10 feet.D. Greater than 10 feet.Correct Answer: B
- A sludge blanket that is too deep in the clarifier can lead to what problem?A. Improved solids settling.B. Reduced oxygen demand.C. Denitrification and solids floating to the surface.D. Increased BOD removal.Correct Answer: C
- What does the Sludge Volume Index (SVI) numerically express?A. The concentration of MLSS in mg/L.B. The rate of oxygen uptake by activated sludge.C. The settling characteristics of activated sludge.D. The hydraulic residence time in the clarifier.Correct Answer: C
- A Sludge Volume Index (SVI) value greater than 250 mL/g typically indicates:A. Normal operation and good settling.B. Old biosolids and possible pin floc.C. Bulking biosolids and poor settling.D. Optimal nutrient removal.Correct Answer: C
- What is the Surface Overflow Rate (SOR)?A. The relationship of the flow into a clarifier to its surface area.B. The mass of solids entering the clarifier per unit time.C. The flow over the effluent weir per unit weir length.D. The depth of the sludge blanket.Correct Answer: A
- If the Solids Loading Rate (SLR) increases above design limits in a secondary clarifier, what is the expected outcome?A. A decrease in effluent solids.B. An increase in effluent solids.C. Improved sludge thickening.D. Reduced energy consumption.Correct Answer: B
- An operator observes a high Weir Overflow Rate (WOR). What is a potential consequence?A. Improved clarifier efficiency.B. Reduced solids carryover.C. Loss of solids, especially with poor settling.D. Increased sludge blanket depth.Correct Answer: C
- What is a common cause of solids washout from the clarifier, especially during high flow periods?A. Low influent BOD.B. Insufficient hydraulic residence time for settling.C. Excessive sludge wasting.D. High dissolved oxygen.Correct Answer: B
- An operator performs a 30-minute settleability test, and the settled sludge volume is very high (e.g., 900 mL/L). A diluted settleability test shows significant improvement. What is the most likely issue?A. Filamentous bulking.B. Excessive old sludge (hindered settling).C. Denitrification in the clarifier.D. Hydraulic short-circuiting.Correct Answer: B
- To optimize secondary clarifier performance, what should be done regarding the effluent weirs?A. Ensure they are uneven to promote mixing.B. Ensure they are level to provide uniform effluent flow.C. Remove them to increase flow capacity.D. Cover them to prevent light penetration.Correct Answer: B
- What is the best long-term strategy for maintaining wastewater treatment during wet weather periods to mitigate hydraulic overloads on clarifiers?A. Continuously increase RAS rates.B. Reduce inflow and infiltration (I/I) into the sewer system.C. Add more chemical coagulants.D. Increase aeration rates in the clarifier.Correct Answer: B
- A plant operator observes a rising sludge blanket and floating sludge clumps in the secondary clarifier. The aeration basin has a low DO concentration at the end. What is the most probable cause?A. High F/M ratio.B. Denitrification in the clarifier due to anoxic conditions.C. Nutrient deficiency.D. Excessive wasting.Correct Answer: B
- Which of the following is a strategy to reduce clarifier solids loading?A. Increase the MLSS concentration in the aeration basin.B. Take all aeration basins offline.C. Operate aeration basins in a step feed configuration.D. Increase the RAS rate to maximum.Correct Answer: C
MLSS/MLVSS Monitoring and Interpretation
- What does MLSS (Mixed Liquor Suspended Solids) represent in the aeration tank?A. Only the active microbial biomass.B. The total concentration of all dissolved solids.C. The total concentration of all suspended solids.D. Only the inorganic suspended solids.Correct Answer: C
- How is MLSS typically measured in a wastewater treatment plant?A. By measuring the volume of settled sludge in a settleometer.B. By filtering a sample through a 0.45-micron filter, then drying and weighing it.C. By measuring the dissolved oxygen concentration.D. By analyzing the pH of the mixed liquor.Correct Answer: B
- What percentage of MLSS does MLVSS (Mixed Liquor Volatile Suspended Solids) typically constitute?A. Less than 20%.B. Around 70%.C. Over 90%.D. It varies too widely to have a typical percentage.Correct Answer: B
- Why is MLVSS considered a better indicator of active microorganisms than MLSS?A. MLVSS includes all suspended solids, active and inactive.B. MLVSS represents the volatile (organic) portion of solids, primarily biomass.C. MLVSS is easier to measure than MLSS.D. MLVSS includes only inorganic solids.Correct Answer: B
- The “pounds formula” (Pounds = Flow (MGD) x Conc (mg/L) x 8.34 lbs/gal) is used to calculate which of the following?A. Only BOD loading.B. Only MLSS in the aeration basin.C. Only solids leaving the system via WAS or effluent.D. All of the above, for various parameters.Correct Answer: D
- A plant has an aeration tank volume of 0.5 MG and an MLSS concentration of 2,500 mg/L. How many pounds of MLSS are in the aeration tank? (Use 8.34 lbs/gal)A. 1,250 lbsB. 10,425 lbsC. 12,500 lbsD. 20,850 lbsCorrect Answer: BCalculation: 0.5 MG * 2,500 mg/L * 8.34 lbs/gal = 10,425 lbs
- If the MLSS concentration is 3,000 mg/L and the volatile solids percentage is 75%, what is the MLVSS concentration?A. 750 mg/LB. 2,250 mg/LC. 3,000 mg/LD. 4,000 mg/LCorrect Answer: BCalculation: 3,000 mg/L * 0.75 = 2,250 mg/L
- A plant receives an influent flow of 2.0 MGD with a BOD concentration of 200 mg/L. What is the BOD loading in lbs/day? (Use 8.34 lbs/gal)A. 1,668 lbs/dayB. 3,336 lbs/dayC. 4,000 lbs/dayD. 8,340 lbs/dayCorrect Answer: BCalculation: 2.0 MGD * 200 mg/L * 8.34 lbs/gal = 3,336 lbs/day
- Why is accurate and timely MLSS/MLVSS data essential for activated sludge process control?A. It is only required for regulatory reporting.B. It provides the essential quantitative data for F/M, MCRT, and RAS/WAS calculations.C. It primarily indicates the presence of pathogens.D. It is used to determine the plant’s hydraulic capacity.Correct Answer: B
- An operator wants to maintain an F/M ratio of 0.35 in an aeration tank with a volume of 0.2 MG. The influent BOD loading is 500 lbs/day. What MLVSS concentration (mg/L) should be maintained? (Use 8.34 lbs/gal)A. 850 mg/LB. 1,200 mg/LC. 1,500 mg/LD. 2,000 mg/LCorrect Answer: ACalculation: Lbs MLVSS = 500 lbs/day / 0.35 = 1428.57 lbs. MLVSS Conc = 1428.57 lbs / (0.2 MG * 8.34 lbs/gal) = 855.9 mg/L (approx. 850 mg/L)
RAS/WAS Optimization and Impacts
- What is the primary function of Return Activated Sludge (RAS) in the activated sludge process?A. To remove excess sludge from the system.B. To provide oxygen to the aeration tank.C. To return active microorganisms from the clarifier to the aeration tank.D. To chemically treat the effluent.Correct Answer: C
- What is a common operational challenge associated with RAS flow?A. Maintaining excessively high dissolved oxygen levels.B. Blockages, maintenance difficulties, and balancing flow rates.C. Eliminating all microbial activity.D. Increasing the sludge blanket depth.Correct Answer: B
- If the RAS concentration is too low, what is a likely impact on treatment performance?A. Increased oxygen demand.B. Excessive sludge buildup.C. Organic materials might not be broken down effectively, leading to poor effluent quality.D. Improved sludge thickening.Correct Answer: C
- What is the primary purpose of Waste Activated Sludge (WAS) in the activated sludge process?A. To increase the F/M ratio.B. To maintain a desired microbial population and prevent overpopulation.C. To return settled solids to the aeration tank.D. To enhance nitrification.Correct Answer: B
- How does WAS management directly influence the activated sludge system?A. It directly controls the hydraulic residence time (HRT).B. It directly controls the Mean Cell Residence Time (MCRT) or sludge age.C. It directly controls the influent BOD concentration.D. It directly controls the effluent pH.Correct Answer: B
- In BNR systems, increased phosphorus removal often leads to what impact on sludge management?A. Significant reduction in sludge volume.B. No change in sludge volume.C. Higher sludge volumes requiring efficient disposal strategies.D. Conversion of sludge into inert material.Correct Answer: C
- A plant has an influent flow of 4.0 MGD, an MLSS concentration of 2,000 mg/L, and a RAS SS concentration of 8,000 mg/L. Calculate the required RAS flow rate in MGD.A. 0.5 MGDB. 1.0 MGDC. 1.33 MGDD. 2.0 MGDCorrect Answer: CCalculation: RAS flow rate = 4.0 MGD * [2,000 / (8,000 – 2,000)] = 4.0 * (2,000 / 6,000) = 4.0 * (1/3) = 1.33 MGD
- A plant has 30,000 lbs of MLSS under aeration and 2,500 lbs/day of suspended solids leaving the system (WAS + effluent). What is the MCRT in days?A. 5 daysB. 8 daysC. 12 daysD. 15 daysCorrect Answer: CCalculation: MCRT = 30,000 lbs / 2,500 lbs/day = 12 days
- What is the effect of decreasing the WAS rate on the sludge age?A. Sludge age decreases.B. Sludge age increases.C. Sludge age remains constant.D. Sludge age becomes irrelevant.Correct Answer: B
- An operator observes that the sludge blanket in the secondary clarifier is consistently too deep, leading to solids carryover. The MLSS in the aeration basin is within the normal range. What is a likely immediate adjustment to make?A. Decrease the RAS rate.B. Increase the WAS rate.C. Increase the influent flow.D. Decrease aeration in the basin.Correct Answer: B
- Which of the following best describes the relationship between RAS and WAS optimization for system stability?A. They are independent parameters, optimized separately.B. They are competing parameters, where one must be maximized and the other minimized.C. They are interdependent, requiring a coordinated strategy for overall system balance.D. RAS primarily controls hydraulic flow, and WAS primarily controls chemical dosing.Correct Answer: C
- An operator aims to select for slower-growing nitrifying bacteria in the activated sludge. What adjustment to WAS would best support this goal?A. Increase WAS rate to shorten MCRT.B. Decrease WAS rate to lengthen MCRT.C. Maintain a constant WAS rate regardless of conditions.D. Eliminate WAS entirely.Correct Answer: B
- Which operational challenge can arise if the RAS concentration is too high?A. Insufficient BOD removal.B. Reduced oxygen demand.C. Excessive sludge buildup and potential system clogging.D. Pin floc formation.Correct Answer: C
- A plant experiences consistent issues with sludge bulking despite adequate aeration. Microscopic examination reveals a low F/M ratio. What operational adjustment should the operator consider?A. Increase the WAS rate.B. Decrease the RAS rate.C. Increase the MLVSS concentration.D. Decrease the MLVSS concentration to increase the F/M ratio.Correct Answer: D
- Effective mixing techniques in aeration tanks contribute to RAS/WAS optimization by:A. Increasing sludge blanket depth.B. Promoting sludge settling in undesirable zones.C. Preventing sludge settling and reducing blockage risks.D. Reducing the need for nutrient removal.Correct Answer: C
Conclusion
This comprehensive guide and accompanying 100-question multiple-choice quiz are meticulously designed to equip candidates with the foundational and advanced knowledge required for success in the Grade IV ABC/WPI Wastewater Certification Exam, particularly focusing on advanced activated sludge processes. The report has elaborated on core concepts, delved into the intricate mechanisms of Biological Nutrient Removal (BNR), nitrification, and denitrification, and explored various advanced process configurations such as MLE, A2/O, and Modified Bardenpho.
Key learnings from this report underscore the interconnected nature of activated sludge process control. It is evident that effective plant operation transcends isolated parameter adjustments; rather, it demands a holistic understanding of how dissolved oxygen levels, sludge age (MCRT/SRT), food-to-microorganism (F/M) ratios, and return/waste activated sludge rates collectively influence microbial population dynamics, treatment efficiency, and sludge settleability. The report highlights that foam and sludge bulking are not merely nuisances but critical diagnostic indicators, whose characteristics directly point to underlying process imbalances. Similarly, the secondary clarifier, often perceived as a simple settling tank, is revealed as a crucial bottleneck whose performance is intrinsically linked to upstream biological processes and overall plant capacity. The quantitative basis for these controls, through MLSS/MLVSS monitoring and associated calculations, forms the bedrock of data-driven process management.
The exploration of advanced configurations demonstrates a sophisticated engineering approach that optimizes multiple treatment objectives—including carbon, nitrogen, phosphorus, pathogen, and heavy metal removal—while simultaneously striving for operational efficiencies in energy consumption and sludge management. The increasing role of automation in aeration control further exemplifies the shift towards dynamic, data-driven optimization, which is critical for consistently meeting stringent effluent limits and reducing operational costs.
For continued professional development, it is recommended that operators not only master the theoretical knowledge presented but also cultivate strong practical skills in microscopic analysis and routine laboratory testing. Continuous learning about emerging technologies, advanced control systems, and troubleshooting methodologies will be invaluable. Furthermore, a commitment to understanding the plant as an integrated system, where each unit operation impacts the others, will empower operators to move beyond reactive problem-solving to proactive optimization, ensuring the sustained health and compliance of wastewater treatment facilities.