Ever thought about how essential a well-maintained wastewater treatment plant is to public health and environmental safety? These facilities rely on rigorous maintenance to ensure efficiency, regulatory compliance, and prevent costly failures. In this guide, learn how to build a robust maintenance program for an activated sludge plant to keep operations smooth and equipment lasting longer.
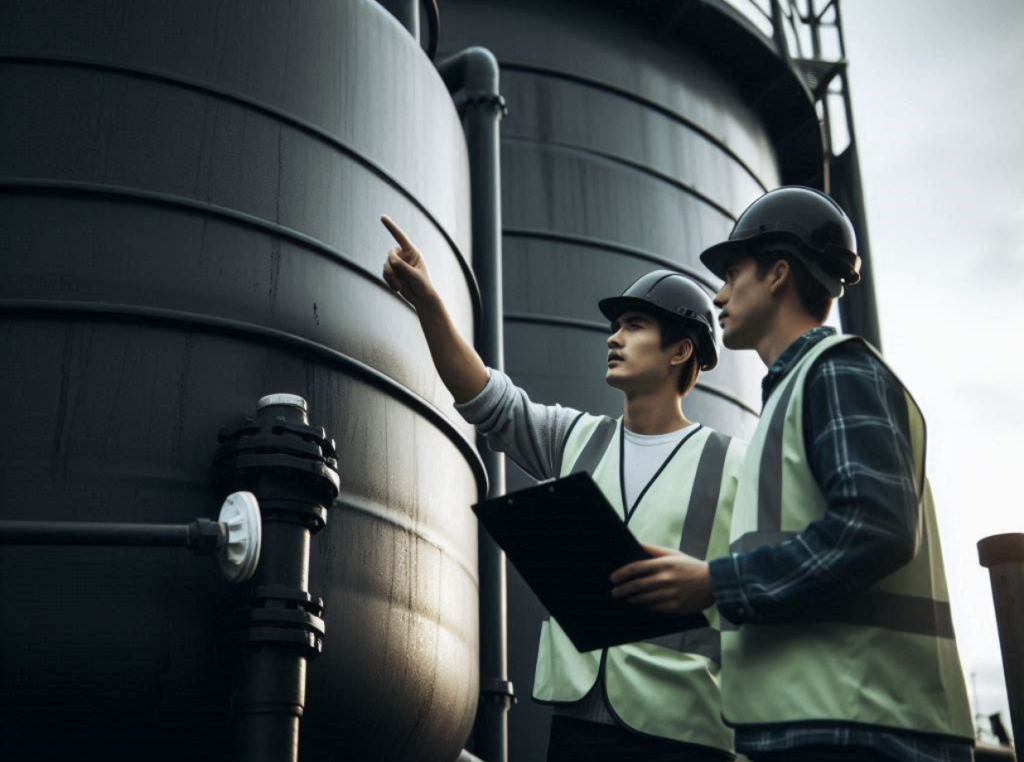
Introduction
Maintenance is the backbone of any successful wastewater treatment operation. It supports plant efficiency, extends the lifespan of equipment, and ensures compliance with stringent environmental regulations. This article presents a structured approach to developing a maintenance program tailored to the needs of activated sludge wastewater treatment plants. By following these guidelines, plant operators, facility managers, and maintenance personnel can significantly improve plant performance and reliability.
Preventive Maintenance
Preventive maintenance refers to routine tasks designed to prevent equipment failures before they occur. These scheduled activities are crucial for ensuring the smooth operation of wastewater treatment plants.
Daily Tasks
Daily maintenance activities are integral to identifying issues before they escalate. They include:
- Visual Inspections: Examination of equipment for signs of wear and tear.
- Lubrication: Ensuring moving parts are well-oiled to prevent mechanical failures.
- Effluent Quality Checks: Monitoring effluent parameters against compliance standards.
Weekly Tasks
Weekly tasks are more detailed inspections that ensure the ongoing health of plant operations:
- Calibration of Sensors: Ensuring measurement devices are precise and reliable.
- Pump and Valve Inspections: Checking for leaks or obstructions.
- Equipment Cleaning: Removing debris buildup that could affect equipment function.
Monthly Tasks
Monthly tasks delve deeper into the assessment of plant equipment, including:
- Comprehensive System Testing: Running tests to ensure all systems are operating within normal parameters.
- Inspection of Electrical Systems: Ensuring electrical components are functioning safely.
- Lubrication of All Machinery: Re-applying lubricants according to the manufacturer’s specifications.
Annual Tasks
Annual maintenance often involves comprehensive assessments and overhauls:
- Major Equipment Overhaul: Inspecting and overhauling major pieces of equipment.
- Infrastructure Evaluation: Assessing the structural integrity of buildings and tanks.
- Review and Update of Maintenance Records: Ensuring all records accurately reflect equipment status and are up-to-date.
Checklists and Schedules
Ensuring these tasks are completed efficiently requires detailed checklists and schedules. Tailor these tools to your facility’s specific needs, documenting each task to ensure nothing is overlooked. Here’s a simplified checklist example for daily tasks:
ask | Status | Comments |
---|---|---|
Visual Inspection | Complete | No issues |
Lubrication of Bearings | Complete | Proper levels |
Effluent Quality Monitoring | Complete | Within limits |
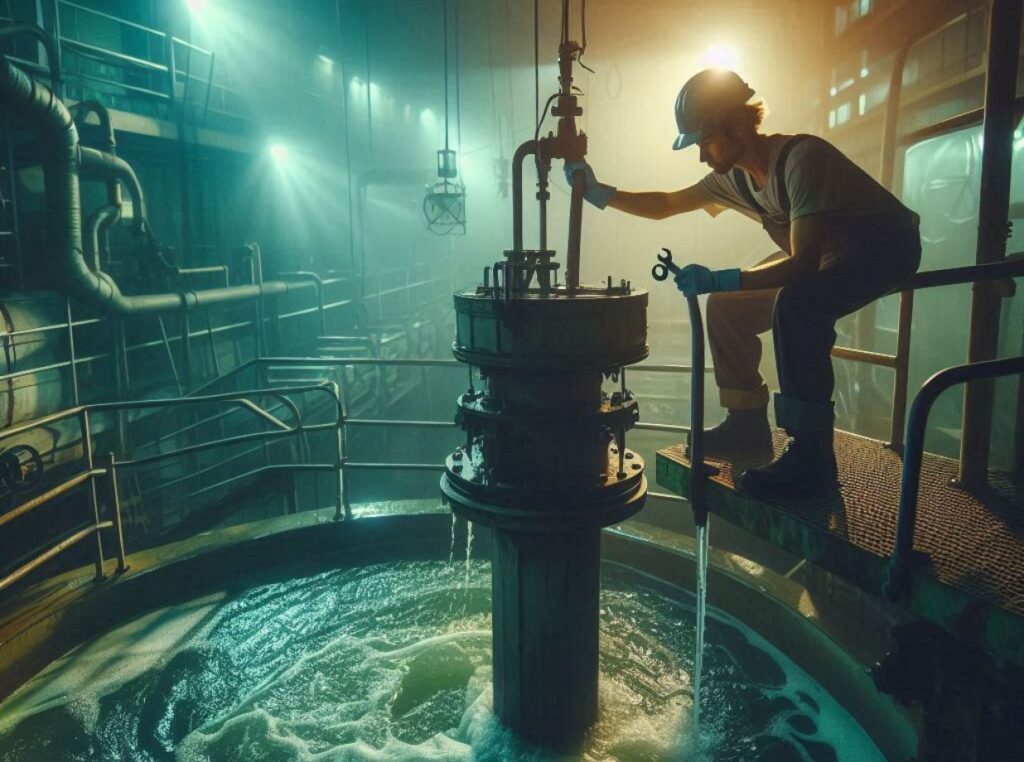
Predictive Maintenance
Predictive maintenance involves anticipating potential equipment failures and addressing them before they occur. This is achieved through advanced tools and techniques.
Condition Monitoring
Utilize sensors and diagnostic software to monitor equipment conditions continually. This method allows for real-time analysis of parameters such as vibration levels, temperature, and mechanical noise.
Diagnostic Testing
Conduct regular diagnostic tests to predict equipment lifespan and identify potential failures. Advanced diagnostic tools can detect subtle changes in equipment performance that may indicate the early stages of wear or malfunction.
Equipment Replacement Planning
Based on predictive analytics, plan for equipment replacement before failures occur. This ensures seamless operations without unexpected downtimes.
Corrective Maintenance
Despite preventive efforts, issues may arise that require corrective actions. Corrective maintenance focuses on addressing these unforeseen problems.
Troubleshooting Procedures
A structured approach to troubleshooting is critical for minimizing downtime. Develop a flowchart for identifying and resolving common issues swiftly to ensure plant operations resume as soon as possible.
Emergency Repair Workflows
Create and implement workflows for emergency repairs, emphasizing speed and efficiency. These should include clear communication channels, predefined roles, and responsibilities so that staff can react promptly.
Quick Response Teams
Form dedicated teams trained to handle emergencies efficiently. These teams should be equipped with the tools and skills required for rapid response and repair.
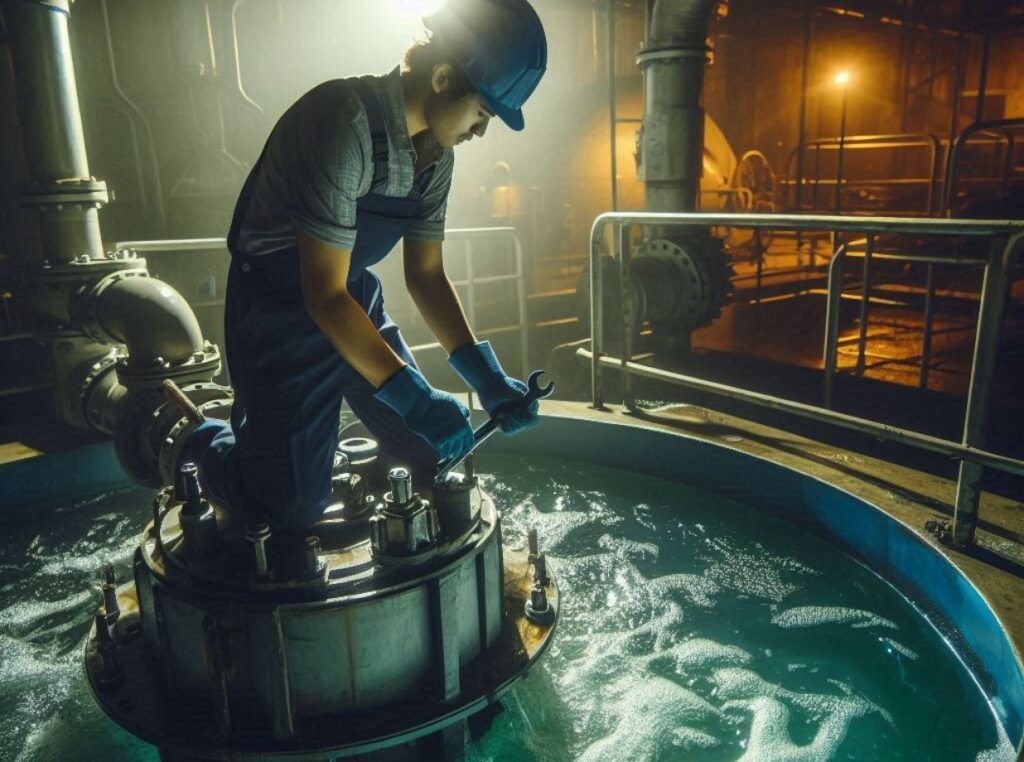
Maintenance Management System (MMS)
An effective Maintenance Management System (MMS) is essential for organizing maintenance tasks and resources.
Work Order System
Implement a work order system to track and manage maintenance activities. This system should capture details on every task, including priority level, resources required, and deadlines.
Digital Recordkeeping
Transition to digital recordkeeping for accessing and updating equipment history, inspection results, and maintenance actions. This ensures data accuracy and availability for all stakeholders.
Inventory Management
Maintain an optimized inventory of spare parts and tools. Regularly update inventory to ensure essential items are available when needed, avoiding unnecessary delays.
Safety and Training
Ensuring plant staff are well trained and adhere to safety standards is non-negotiable in maintaining a wastewater treatment plant.
Safety Protocols
Implement rigorous safety protocols based on OSHA and environmental regulations. These should include personal protective equipment (PPE) requirements, emergency exit plans, and hazard communication standards.
Training Needs
Regularly assess training needs for staff to ensure they are equipped with the latest knowledge and skills. This includes understanding new technologies and regulatory changes affecting wastewater treatment.
Compliance with Standards
Ensure compliance with all relevant OSHA and environmental regulations. Non-compliance can lead to significant penalties and operational shutdowns.
Review and Improvement
No maintenance program is complete without regular assessments to identify areas for improvement.
Routine Audits
Conduct routine audits to evaluate the effectiveness of maintenance practices. These audits should assess task completion rates, equipment performance, and compliance levels.
KPI Tracking
Establish Key Performance Indicators (KPIs) to track maintenance efficiency and effectiveness. These could include downtime reduction, cost savings, and work order completion rates.
Budget Assessments
Regularly evaluate maintenance budgets to ensure optimum use of resources. This includes identifying areas for cost savings and ensuring that there is adequate funding for preventive and corrective maintenance activities.
Conclusion
A comprehensive wastewater treatment plant maintenance program is your safeguard against operational inefficiencies, regulatory non-compliance, and premature equipment failures. By implementing a structured approach encompassing preventive, predictive, and corrective maintenance, and supported by a robust Maintenance Management System, you can ensure the longevity and reliability of your facility. Prioritizing safety and continuous improvement becomes a collaborative journey towards sustainability and operational excellence, benefiting both the community and the environment.